MANUTENÇÃO PREDITIVA – GENERALIDADES
1 – MANUTENÇÃO PREDITIVA – GENERALIDADES
A manutenção preditiva , na sua generalidade, é o tema tratado neste artigo.
O meio mais simples de operar com máquinas consiste em deixá-las trabalhar até pararem por avaria e então repará-las de modo a ficarem aptas para novo período de serviço. Esta prática pode tornar-se muito cara em termos de perdas de produção e custos de manutenção, para além de poder pôr em risco a segurança das pessoas e o ambiente.
Hoje em dia é geralmente aceite que, no caso de unidades com grandes investimentos de capital, é mais satisfatório do ponto de vista económico, implementar acções de manutenção regulares. Estas, envolvem a revisão das máquinas ou das suas componentes a intervalos regulares, de modo a reduzir a probabilidade de ocorrência de avarias durante o período em que os equipamentos se encontram disponíveis. O principal problema a ultrapassar na implementação deste tipo de manutenção, reside na escolha do intervalo de tempo apropriado, entre revisões. Efectivamente, o intervalo ao fim do qual se torna essencial uma acção de manutenção não é constante, variando de uma ocasião para a outra, devido a diferenças nas condições de serviço e comportamento de componentes.
A figura mostra o comportamento de um grupo de máquinas “típico” se não se proceder a manutenção preventiva. Por outras palavras, o padrão típico de ocorrência de avarias, em Manutenção Curativa.
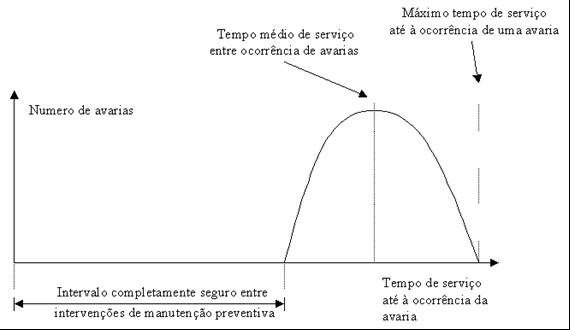
Pode-se ver que existe um intervalo de tempo seguro, entre revisões, de modo a se evitarem todas as avarias antes destas poderem ocorrer. Contudo, caso se escolha este intervalo, ir-se-ão efectuar intervenções muito antes delas serem efectivamente necessárias. Existirão, portanto, muitos casos em que as máquinas poderiam trabalhar mais tempo sem ocorrer uma paragem por avaria. Esta prática desperdiça tempo de serviço e por aumentar a frequência das intervenções, aumenta a incidência de erros humanos nas montagens.
Uma aproximação mais satisfatória, em termos económicos, é a de executar a manutenção preventiva, a intervalos que podem ser irregulares, fazendo depender as intervenções da condição de funcionamento das máquinas. Para se proceder a esta manutenção “sob condição”, também designada de “Manutenção Preditiva”, é essencial conhecer o estado de funcionamento dos equipamentos e a sua evolução com o tempo. Para tal se efetivar, é necessário a existência de um sistema de controle de condição que forneça este conhecimento.
Esta aproximação considera cada máquina individualmente. Substituindo revisões a intervalos fixos, por inspecções a intervalos fixos, a evolução na condição de funcionamento de cada máquina pode ser seguida de perto.
O axioma base da Manutenção Preditiva é o de que só se intervém nas máquinas quando os resultados das inspecções evidenciam que isto é necessário. Isto está também de acordo com a sensibilidade da maioria das pessoas no que se prende a ser insensato mexer em máquinas a funcionarem bem.
Por exemplo, com a medição regular dos níveis de vibrações de uma bomba, os sintomas de avarias podem ser detectados e seguido o seu desenvolvimento. Os resultados das medidas podem ser extrapolados de maneira a predizer a altura em que se vão atingir níveis inaceitáveis e, portanto, quando se deve intervir, como se pode ver na figura a seguir apresentada..

2 – VANTAGENS DA MANUTENÇÃO PREDITIVA
2.1 – Vantagens Económicas da Manutenção Preditiva
As vantagens económicas da Manutenção Preditiva surgem genericamente da seguinte forma:
- 2/3 dos ganhos a partir da redução de perdas de produção
- 1/3 dos ganhos a partir da redução de custos de manutenção
Estas proporções correspondem a:
- Redução das perdas de produção correspondendo a 75% de dias perdidos anualmente quando a manutenção Preditiva não é usada
- Redução em 5% do custo total de manutenção
A razão pela qual só se podem esperar 75% de redução de perdas de produção, é a de que alguns tipos de avarias, independentemente de serem detectadas, exigem que a produção seja interrompida. Por outro lado, não se pode esperar que o controlo de condição seja 100% eficiente.
O número de 5% para redução de custos de manutenção surge a partir do facto da maioria da poupança ser em custo de mão de obra de manutenção curativa. Visto o custo da reparação curativa ser geralmente cerca de 1/3 do custo total da manutenção e destes, 1/3 ser custos de mão de obra, o custo de mão de obra na manutenção curativa é cerca de 10% do total. Uma redução para metade dá o número de 5%.
Na figura a seguir estão ordenados os diferentes tipos de indústria, por ordem crescente de suscetibilidade, de haver ganhos com a Manutenção Preditiva. (resultados de um estudo levado a cabo na Grã-Bretanha em 1978)

Seguidamente apresentam-se alguns exemplos de aplicação de manutenção Preditiva.
Exemplo 1 – Indústria de Processo / Refinaria
Na figura a seguir apresentada pode-se ver o número de paragens devido a problemas em máquinas rotativas numa refinaria.
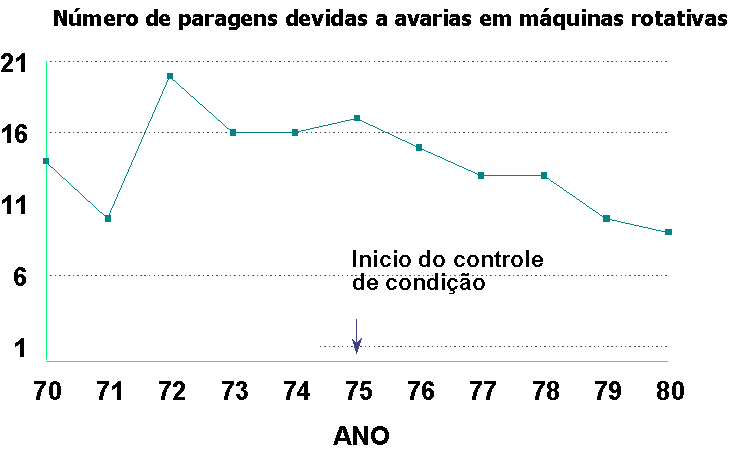
Na figura a seguir apresentada pode-se ver o número médio de horas necessárias para arrancar depois devidas a máquinas rotativas numa refinaria.
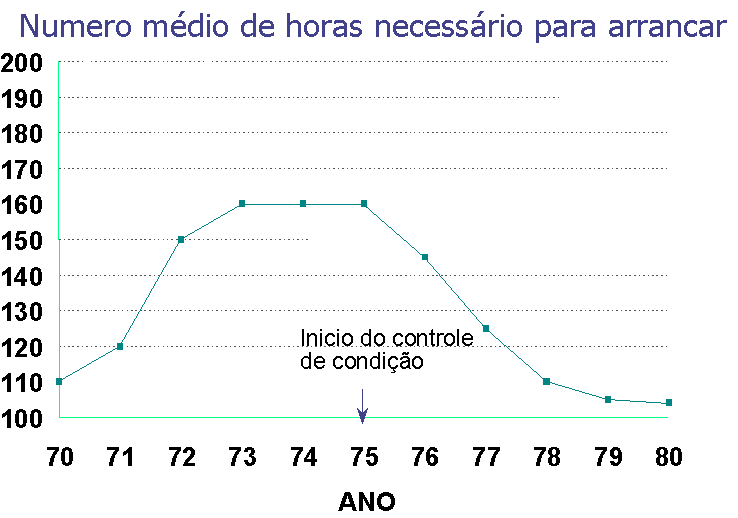
Exemplo 2 – Oficina de Reparação de Motores Eléctricos
Na figura a seguir apresentada pode-se ver a taxa de reprovações em ensaios de motores elétricos depois de revisão. Em 1978 implementou-se um programa de aceitação de motores depois da revisão.
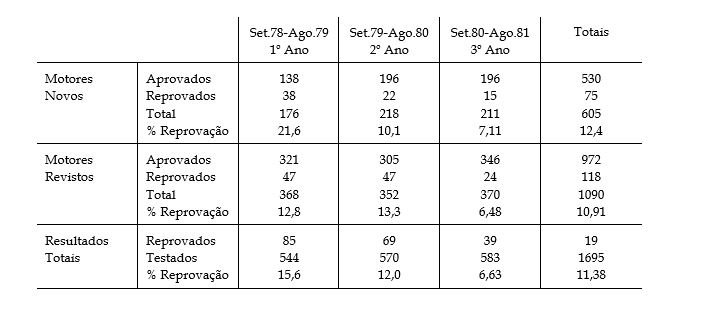
Note-se a descida acentuada do número de motores em mau estado, ao longo dos anos.
1978 | 1981 | |
Motores elétricos Pessoal Horas extraordinárias Custo de mão de obra por ano Contratos exteriores por ano | 1171 7 20% $ 462 000 $ 1 272 000 | 2300 3 negligível $ 150 000 $ 860 000 |
Exemplo 3 – Custo de Manutenção por Cavalo por Ano – Geração de Energia
Na figura a seguir apresentada pode-se ver o custo de manutenção por cavalo por ano na indústria de geração de energia.

Exemplo 4 – Paragens devidas a avarias em máquinas rotativas, em duas máquinas de papel
Na figura a seguir apresentada pode-se ver o número paragens devidas a avarias em máquinas rotativas em duas máquinas de papel, antes e depois de se inicitar um programa de manutenção preditiva.
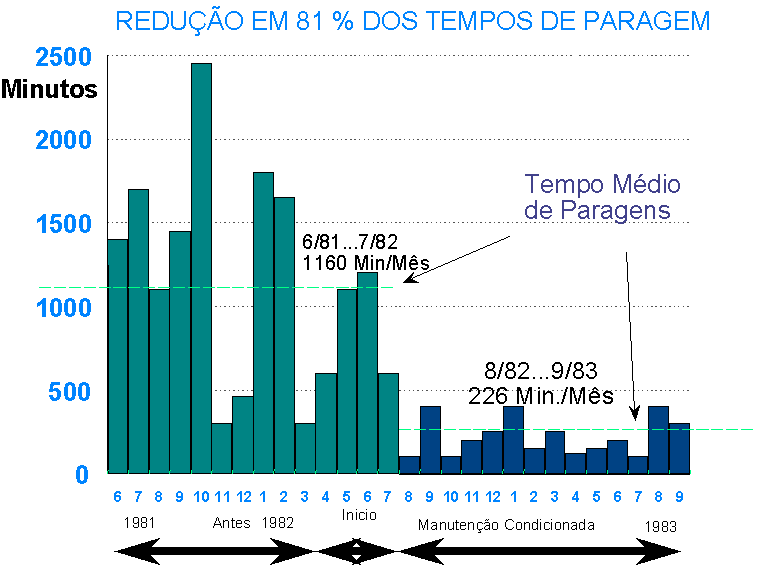
2.2 – Outras Vantagens da Manutenção Preditiva
As vantagens económicas não são o único ponto de vista válido a considerar quando a implementar, ou não, um sistema de Controle de Condição. Visto existirem vantagens de diversa ordem, em cada caso concreto existirão factores particularmente favoráveis ou desfavoráveis para a Manutenção Preditiva.
Estes estão listados nos quadros que vêm a seguir.
QUADRO I
Controlar a condição das máquinas pode dar os seguintes benefícios | Maneira como os benefícios aparece |
1) Aumento da segurança do operador da máquina | O tempo de aviso dado pelo controle da condição permite parar as máquinas antes de atingirem um estado crítico, especialmente se elas não poderem parar instantaneamente |
2) Aumentar a disponibilidade dos equipamentos resultando em maior produção a partir do capital investido 3) Reduzir custos de Manutenção | O tempo de serviço das máquinas pode ser aumentado através da maximização do tempo entre revisões. A duração da revisão pode ser diminuída porque a natureza do problema é conhecida, os sobressalentes e pessoal estão disponíveis. Os danos resultantes de avarias podem ser reduzidos ou eliminados. |
4) Maior eficiência na Condução das instalações, permitindo regular o volume da produção às condições das instalações, e atingir um nível de qualidade estável | A carga e velocidade de algumas máquinas pode ser variada para obter um bom compromisso entre produção e tempo de serviço até à próxima beneficiação |
5) Maior capacidade de diálogo com fabricantes de máquinas e equipamentos ou reparadoras, baseado nos conhecimentos obtidos a partir do controle de condição | A inspecção de um equipamento novo, no fim da garantia e depois de revisões fornece úteis bases de comparação |
6) Melhores relações com os clientes devido à redução de paragens de produção imprevistas | O tempo de aviso antes da avaria, obtido através da informação fornecida pelas inspecções, permite que isto se realize |
7) Possibilidade de melhorar a especificação e projecto de futuras instalações | O histórico obtido através das inspecções pode servir para este fim |
Fatores favoráveis à aplicação, com sucesso da manutenção Preditiva, numa fábrica, máquina ou equipamento.
QUADRO II
Onde houver um risco para a segurança associado à avaria de uma máquina | Exemplos típicos são os de fábricas que trabalham com produtos perigosos e meios de transporte de pessoas |
Onde for necessário um rigoroso planeamento da manutenção | Exemplos típicos são os de equipamento em locais remotos só ocasionalmente visitado para manutenção, ou equipamento móvel que faça só visitas ocasionais à sua base de apoio |
Onde a fábrica ou equipamento for de um projecto novo onde ainda permanecem alguns problemas de desenvolvimento | A inspecção permite detectar as avarias no seu início, enquanto os danos são ligeiros, de maneira a estar disponível informação importante para guiar melhorias ao projecto |
Onde máquinas de grande custo, sujeitas a riscos de avarias avultadas, forem operadas por pessoal com pouca formação ou remotamente | O controle de condição permite detectar o problema com tempo de aviso suficiente para emitir instruções para retirar o equipamento de serviço, antes de ocorrerem danos graves |
Onde o fabricante do equipamento estiver em condições de oferecer um serviço de controle de condição a diversos utilizadores do equipamento | O custo para cada utilizador pode deste modo ser reduzido, e o fabricante recebe um importante retorno de informação para dirigir o projecto e desenvolvimento do seu produto |
Onde a instrumentação ou outro equipamento requerido para a inspecção for, ou já estiver a ser, usado para outro fim | Outra aplicação da instrumentação ou equipamento pode ser o controlo de processo ou outras actividades como equilibragem ou diagnóstico |
3 – FACTORES DE INSUCESSO
Factores que são desfavoráveis à aplicação com sucesso de Manutenção Preditiva, a uma fábrica, máquina ou equipamento.
QUADRO III
Onde a indústria estiver com pouca carga e a fábrica ou máquina estiver frequentemente parada | Se a fábrica estiver frequentemente parada, há geralmente muitas oportunidades para inspecção e manutenção durante as paragens |
Onde o grupo de máquinas similares for demasiado pequeno para permitir a acumulação da experiência necessária à eficaz interpretação das leituras e correctas tomadas de decisão sobre o seu significado | Para acumular experiência num período de tempo razoável, o número mínimo varia geralmente entre 4 a 10 dependendo do tipo de máquina ou componente. O problema pode ser resolvido partilhando os serviços da inspecção com outras fábricas, envolvendo os fabricantes das máquinas ou serviços externos |
Onde operadores muito qualificados tiverem contacto apertado com as suas máquinas, e puderem usar os seus sentidos para elaborar uma tendência subjectiva | Máquinas ferramentas e navios podem ser exemplo desta situação, mas qualquer passo no sentido de usar operadores menos qualificados, favorece a aplicação da manutenção Preditiva |
Onde as intervenções em máquinas ou equipamentos móveis forem feitas em alguns centros onde a mão de obra especializada estiver instalada | A principal função do controlo de condição nestas circunstâncias é a de determinar as prioridades para intervenções nas diversas unidades. A manutenção Preditiva neste caso, tem um efeito económico reduzido, a menos que possa resultar em aperfeiçoamento do projecto ou aumento de rendimento, e assim resultar na redução da frequência de intervenções e custos |
4 – O CONTROLO DE CONDIÇÃO
Existem fundamentalmente dois métodos para se proceder ao controlo de condição:
- Acompanhamento da tendência;
- Verificação da condição de funcionamento
O acompanhamento da tendência consiste na medição periódica ou em contínuo, de um parâmetro indicador das variações da condição de funcionamento da máquina ou das suas componentes. É, portanto, evidente, que é necessário proceder à seleção de indicadores significativos da deterioração da máquina ou componentes, como sejam alguns indicados na página a seguir.
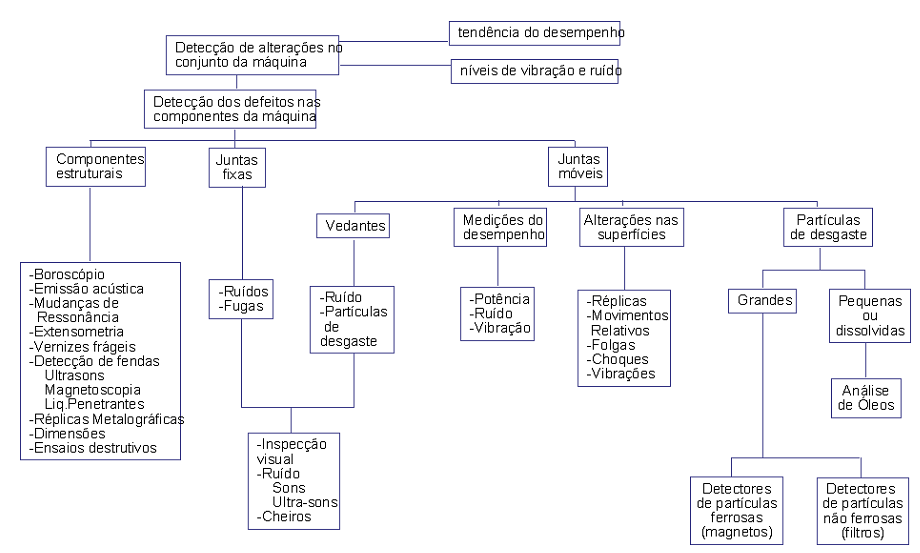
Com base nos valores medidos, elabora-se uma tendência que permite determinar quando a degradação de uma máquina excede um estado crítico, como mostra a figura.
Os princípios envolvidos estão ilustrados na figura a seguir, que mostra o meio através do qual o acompanhamento da tendência pode dar um tempo de aviso antes da deterioração atingir um nível no qual a máquina tenha que ser posta fora de serviço.

O tempo de aviso antes da avaria ocorrer, é uma das principais vantagens de usar o acompanhamento de tendência em vez de alarmes ou relés de protecção.
A verificação da condição, tem lugar através da medição de um parâmetro, numa determinada altura, inferindo-se deste modo o estado da máquina. Para ser efectiva, a medição tem que ser precisa, quantificável devendo também ser conhecidos valores limites a não exceder por mais de um certo número de horas de serviço. Os valores limites, para serem estabelecidos, requerem uma larga experiência anterior com o tipo particular de máquina em causa. A verificação da condição é, portanto, menos flexível que o acompanhamento de tendência, especialmente no que se refere ao tempo de aviso antes da avaria.
Pode ser, no entanto, muito útil em situações onde existam diversas máquinas a trabalhar em conjunto, visto neste caso, poderem ser feitas comparações entre as máquinas em serviço e as máquinas novas ou que se sabem em boas condições.
Estes dois métodos de controlo de condição estão comparados em maior detalhe no quadro a seguir apresentado.
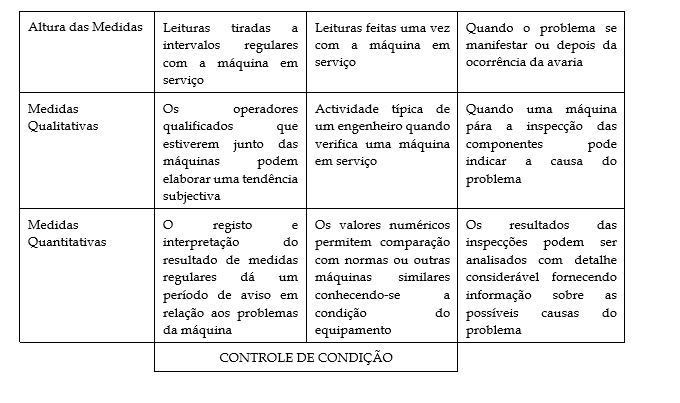
5 – AS AVARIAS
Na sua forma mais simples, avaria, pode ser definida como qualquer modificação numa parte ou componente de uma máquina que a impeça de desempenhar a sua função satisfatoriamente.
Os estados habituais precedendo uma rotura final são, “avaria incipiente”, “dano incipiente”, “deterioração” e “dano”, qualquer um deles, podendo tornar a parte ou componente não fiável ou insegura para serviço.
As avarias podem também ser classificadas do seguinte modo:
- Deficiências de projeto
- Defeitos de material
- Defeitos de fabrico
- Defeitos de montagem
- Condições de serviço fora de projecto
- Deficiência de manutenção
- Erros de operação
Na tabela a seguir apresentada encontram-se os tipos básicos de modos de avaria encontrados em 99% das roturas em equipamentos de unidades petroquímicas.
Classificação dos Modos de Avaria
- Deformação – plástica, elástica, etc.
- Fractura – fendas, fadiga, picadas, etc.
- Modificações da superfície – fendas, cavitação, desgaste, etc.
- Mudanças no material – contaminação, corrosão, desgaste, etc.
- Deslocamentos – desapertos, folgas excessivas, etc.
- Fugas
- Contaminações
Modo de avaria, não deve ser confundido com causas de avaria, porque a primeira é o efeito e a segunda a causa. O modo de avaria pode ser também a consequência de uma longa cadeia de causa, efeito, levando finalmente a uma avaria funcional, isto é, um sintoma, um problema ou insuficiência operacional referente a uma parte de um equipamento como entidade única.
Os meios básicos das roturas em componentes e partes de máquinas são sempre força, tempo, temperatura e ambiente, como indicado na tabela a seguir apresentada.
Causas da Rotura de Componentes e Partes de Máquinas
Força | estática transiente cíclica | Temperatura | baixa ambiente elevada estacionária transiente cíclica |
Tempo | muito curto curto longo | Ambiente | químico nuclear |
Do ponto de vista da inspecção as avarias reflectem-se em deficiências de diversa ordem.
No quadro a seguir apresentado encontram-se listados sintomas de avarias típicas em equipamentos de processo.
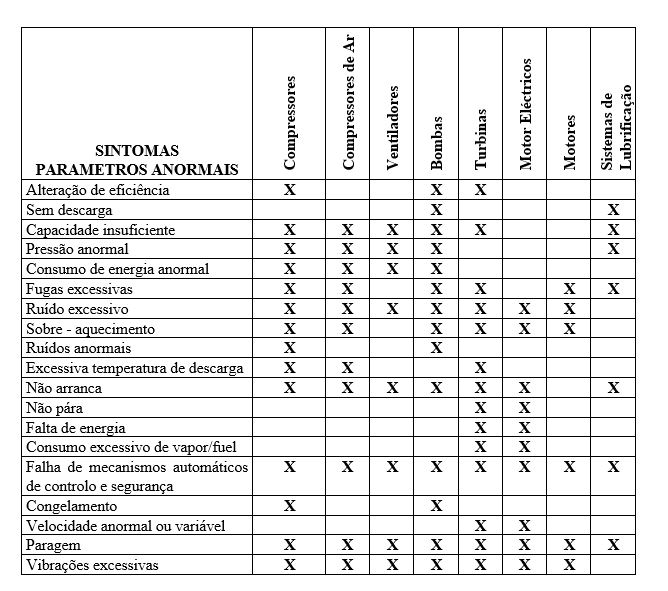
A função da inspeção é acompanhar os equipamentos de maneira a detetar os sintomas de avarias.
6 – TÉCNICAS DE CONTROLO DE CONDIÇÃO
A base de um sistema de controlo de condição é constituída pelas acções de inspecção que regularmente tem lugar nas máquinas e equipamentos.
Estas acções, em que estão em jogo não só os sentidos do inspector, mas também diversas técnicas específicas, tem por fim determinar a evolução das condições de serviço dos equipamentos.
Entre as técnicas de inspecção existentes, podem-se referir por exemplo as seguintes:
- Nível global
- Choques
- Espectro de frequência
– Controle de Desgaste
- Análise de óleos
- Detetores de partículas
- Ferrografia
– Controle de Temperaturas
- Termometria
- Termografia
– Controle de Ruídos
– Controle de Fugas
Cada uma delas tem vantagens e defeitos, para além das suas limitações próprias. A sua aplicação implica, portanto, um conhecimento de todos os factores em jogo, sendo comum aplicar-se mais de uma técnica em cada máquina, quer como parâmetro para acompanhamento de uma tendência, quer para verificação da condição.
Quando se selecciona uma técnica de controlo para uma máquina crítica, é importante notar que as máquinas se avariam porque uma ou mais componentes críticas falham.
Assim sendo, os métodos mais sensíveis de inspecção de uma máquina, funcionam através de detecção de sintomas de avaria em componentes individuais, visto o maior desvio das condições normais estar concentrado nesses sintomas tornando a anomalia mais fácil de detectar.
A selecção de um método de controlo depende assim do tipo de componentes mais susceptíveis de se avariar e do modo como isto ocorre. Podem-se então considerar as hipóteses possíveis de controlar a degradação dessas componentes e poderá até ser possível encontrar uma só técnica que possa detectar todo o tipo de avarias prováveis numa máquina com uma eficácia razoável.
Por outro lado, a situação específica da manutenção de cada unidade industrial vai impor alguns constrangimentos na escolha das técnicas de inspecção a implementar.
Concretamente no caso dos equipamentos dinâmicos os diversos métodos de inspecção podem-se agrupar do seguinte modo.
1 – Controle Sensorial As máquinas são inspeccionadas utilizando os sentidos humanos
2 – Controle do Rendimento A condição de uma máquina ou componente é aferida através do modo em que está a executar a sua função.
3 – Controle de Vibrações A condição das componentes móveis é aferida pela dimensão e tipo de vibrações geradas.
4 – Controle de Partículas A condição de superfícies de componentes críticas, sujeitas a cargas e movimentos relativos, é avaliada através da recolha e exame das partículas de desgaste geradas.
Os quatro métodos de controle mencionados, são utilizados, detectando a existência de um problema através do nível geral da medida, e na taxa de variação, enquanto a natureza do problema pode ser geralmente determinada a partir de uma análise mais detalhada dos resultados das medidas. Isto é descrito no quadro a seguir apresentado.
Os métodos de controle descritos, são de facto um meio de comunicação entre a máquina e o responsável do controle de condição. A inspecção visual, em relação aos outros métodos, requer uma preparação técnica mínima, devido a ser executada através dos sentidos do inspector. Nos outros métodos, usam-se meios para além dos sentidos humanos, tornando-se mais complexas as intervenções.
É ainda de referir que são sempre de utilizar, de preferência, parâmetros não intrusivos nos sistemas, ou seja, que não interfiram com o processo da máquina e que se possível sejam obtidos durante o seu funcionamento.
REFERÊNCIAS
1 – Condition Monitoring Methods and Economics, Bruel & Kjaer
2 – Pratical Machinery Management for Process Plants VOL.2, Machinery Analysis and Troubleshooting, Heinz P. Bloch, Fred K. Geitner, Gulf P. C.