Instrumentação de supervisão de turbinas
1 Introdução – Instrumentação de supervisão de turbinas (TSI)
Este artigo faz uma introdução à instrumentação de supervisão de turbinas.
Este artigo pertence a uma série, que constitui o material de suporte do curso de análise de vibrações em turbomáquinas. As ligações para os outros artigos podem ser encontradas aqui.
A passagem do vapor para o gás
Em tempos, a maior parte da produção mundial de energia elétrica era proveniente de turbinas a vapor acopladas a geradores. Quer o vapor fosse produzido pela queima de combustíveis fósseis convencionais, como o carvão, o gás ou o petróleo, quer pelo calor da fissão nuclear num reator, o processo era essencialmente o mesmo: aquecer a água até ao vapor, expandi-la através de uma turbina acoplada a um gerador e reciclar o vapor/água esgotado para aquecê-lo novamente através da caldeira ou do reator.
Atualmente, os métodos de produção para satisfazer a procura global de energia mudaram em grande medida para as turbinas a gás em vez das turbinas a vapor, aumentadas por uma percentagem muito mais elevada de fontes renováveis (eólica, solar, geotérmica).
Esta mudança ocorreu por duas razões: as turbinas a gás são mais eficientes do que as turbinas a vapor na extração de energia a partir de uma determinada quantidade de combustível e as turbinas a gás criam menos poluentes (emissões por MW de produção).
As turbinas a gás mais eficientes do mundo, por exemplo, podem atualmente atingir eficiências próximas dos 45%. Em comparação, as centrais compostas apenas por turbinas a vapor raramente ultrapassam os 35% de eficiência.
A persistência das turbinas a vapor
De qualquer modo, existe ainda uma base instalada considerável de turbinas a vapor em todo o mundo e continuará a existir num futuro previsível. Além disso, a instalação de novas turbinas a vapor continuará, uma vez que o calor residual dos gases de escape de uma turbina a gás pode ser utilizado para ferver água e criar vapor para uma turbina a vapor. Estas centrais são conhecidas como instalações de “ciclo combinado” porque combinam os ciclos termodinâmicos das turbinas a gás e a vapor na produção de eletricidade. Consequentemente, são mais eficientes do que as chamadas centrais de “ciclo simples” – quer sejam compostas apenas por turbinas a gás (eficiência típica de 35-40%) ou apenas por turbinas a vapor (eficiência típica de 30-35%).
Em contrapartida, uma central de ciclo combinado típica tem uma eficiência de 50-60%. Esta eficiência acrescida deve-se ao facto de o calor da turbina a gás, que anteriormente subia pela chaminé de escape, ser encaminhado através de um HRSG (Heat Recovery Steam Generator).
O vapor resultante é expandido através de uma turbina que aciona outro gerador elétrico, produzindo mais energia sem a necessidade de qualquer combustível adicional. Um teor idêntico de combustível numa central de ciclo combinado produz, assim, mais MW de eletricidade do que numa central de turbinas a gás de ciclo simples de dimensão semelhante.
O tamanho é importante
Uma das formas de otimizar a eficiência da turbina a vapor é através do tamanho. Uma grande turbina a vapor é mais eficiente do que várias pequenas turbinas a vapor operando em paralelo para produzir uma potência equivalente. Numa central elétrica alimentada a combustíveis fósseis, uma turbina a vapor típica tem dimensões que variam entre 50 MW e 1200 MW (Figura 1.1). Numa central nuclear, uma turbina a vapor típica tem uma dimensão que varia entre 800 MW e 1770 MW. A enorme dimensão destas máquinas significa que os rotores são frequentemente muito longos. Além disso, como o invólucro de uma turbina a vapor é concebido como um recipiente sob pressão, é normalmente muito espesso (300 mm ou mais) e expande-se/contrai-se mais lentamente do que o rotor. Estes e outros fatores combinam-se para resultar num conjunto de medições que são exclusivas dos grandes geradores de turbinas a vapor e complementam a vibração radial convencional, a referência de fase, a temperatura da chumaceira e as medições da posição axial típicas de todas as máquinas rotativas com chumaceiras de película fluida.
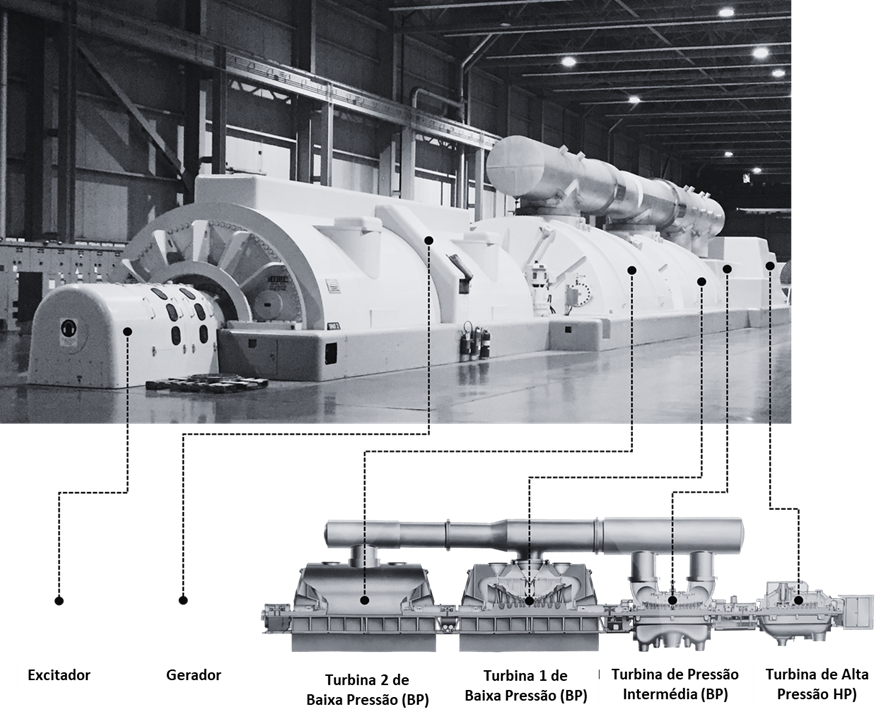
Instrumentação de supervisão de turbinas – Figura 1.1 Um gerador de turbina a vapor de 525MW constituído por corpos de Alta Pressão (AP), Pressão Intermédia (PI) e Baixa Pressão BP) (dois), juntamente com gerador e excitatriz. O vapor entra na caixa da turbina de Alta Pressão pela parte inferior e sai pela parte superior, onde flui para as duas turbinas de Baixa Pressão em paralelo.
2 Instrumentação de supervisão de turbinas – Medições especializadas
As medições especializadas exclusivas dos geradores de turbinas a vapor são efectuadas com a chamada Instrumentação de Supervisão da Turbina (TSI) e são descritas abaixo. Essas medições, juntamente com as medições convencionais de vibração, posição, temperatura e referência de fase, são mostradas na Figura 2.
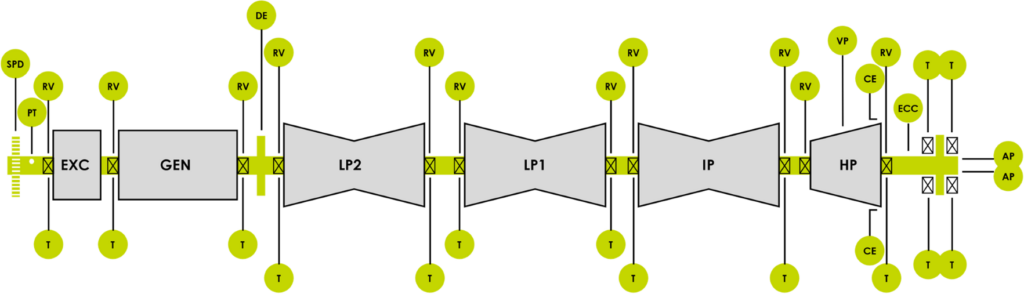
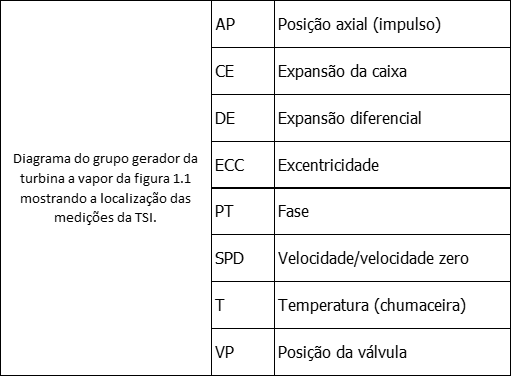
Instrumentação de supervisão de turbinas – Figura 1.2 – Diagrama do grupo gerador da turbina a vapor da figura 1.1 mostrando a localização das medições da TSI
Expansão diferencial (DE)
Tal como referido anteriormente, as grandes turbinas a vapor têm carcaças maciças, relativamente ao seu rotor, o que resulta em diferentes taxas de expansão térmica. Isto deve-se, em parte, às diferenças na metalurgia e aos correspondentes coeficientes térmicos de expansão, mas também às diferenças extremas de massa e inércia térmica entre o rotor (relativamente) leve e a sua carcaça muito mais pesada.
Quando o vapor superaquecido é introduzido numa turbina, as suas carcaças e rotores expandem-se a taxas diferentes. Se a expansão destas partes em relação umas às outras não for rigorosamente medida e controlada, as partes rotativas (por exemplo, as pás da turbina) podem entrar em contacto com as partes não rotativas (diafragmas da turbina) e podem ocorrer danos substanciais.
Para maximizar a eficiência das turbinas a vapor, as folgas entre as pás e os diafragmas são – por projeto – bastante apertadas e apenas uma pequena quantidade de movimento diferencial pode ser tolerada.
As medições de expansão diferencial são frequentemente feitas perto da carcaça de baixa pressão porque o veio é limitado axialmente no local do mancal de impulso (perto da turbina de alta pressão) e então cresce (expande) para fora a partir desse ponto ao longo do comprimento da máquina através das carcaças de PI e BP.
No entanto, a localização pode variar dependendo da caixa da turbina que está a ser medida para a expansão diferencial. Por exemplo, a máquina da Figura 1.1 tem a medição da expansão diferencial no lado externo da turbina AP, como mostrado na Figura 1.2. Independentemente de onde o local de medição da DE é encontrado, o princípio é o mesmo: verificar o crescimento térmico relativo entre a carcaça da turbina e o rotor.
Como a quantidade de expansão térmica pode ser substancial, e além da faixa linear da maioria das sondas de proximidade convencionais, muitas vezes é necessário usar um arranjo especial de duas sondas para abranger toda a faixa de expansão diferencial.
No entanto, nalguns casos, apenas um único transdutor pode abordar a gama necessária – particularmente quando são utilizados os chamados sensores de “gama alargada”. Cada tipo de medição de expansão diferencial é descrito a seguir.
Expansão diferencial de canal único (Colar) SCDEC
Esta medição é efetuada utilizando uma única sonda de proximidade, fixada à caixa da máquina, e observando um colar especial destinado especificamente à medição DE (Figura 2). O espaço entre a ponta da sonda e a superfície perpendicular do colar observado representa o movimento relativo entre a carcaça e o rotor.
Nota: Quando a sonda é fixada rigidamente à base da máquina, em vez de à caixa da máquina, a contribuição devida à expansão da caixa é removida da medição. Isto é conhecido como expansão do rotor, uma vez que indica a quantidade de crescimento/encolhimento absoluto apenas do rotor, em vez da sua relação com a caixa, que também pode crescer/encolher.
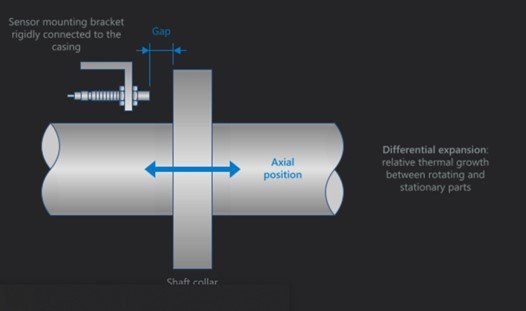
Instrumentação de supervisão de turbinas – Figura 2 Captura de ecrã do software de configuração do VM600MK2 (VibroSight PROTECT) que representa uma medição de Expansão Diferencial de Canal Único (Colar).
Expansão diferencial de canal único (pêndulo) SCDEP
Esta medição é efetuada através de um pêndulo especial que altera o ângulo do alvo da sonda à medida que o veio se expande ou contrai em relação à caixa da máquina.
O ângulo muda por meio de um íman no colar do veio que puxa o pêndulo em qualquer direção à medida que o veio cresce ou encolhe. Utilizando as relações trigonométricas entre as várias geometrias da disposição sonda/alvo, as alterações na abertura da sonda são convertidas na expansão diferencial real. Desta forma, pode ser observada uma gama muito maior de expansão do que se a sonda estivesse simplesmente a observar um colar perpendicular. Ver Figura 3.

Instrumentação de supervisão de turbinas – Figura 3 – Captura de ecrã do software de configuração VM600Mk2 (VibroSight PROTECT) que representa uma medição SCDEP. Na imagem inferior, o eixo expandiu-se para a esquerda, rodando o pêndulo no sentido dos ponteiros do relógio e aumentando o espaço da sonda (Espaço 2 > Espaço 1).
Expansão diferencial de canal duplo (colar) DCDEC
Esta medição utiliza duas sondas: uma virada para a outra e observando lados opostos do colar DE.
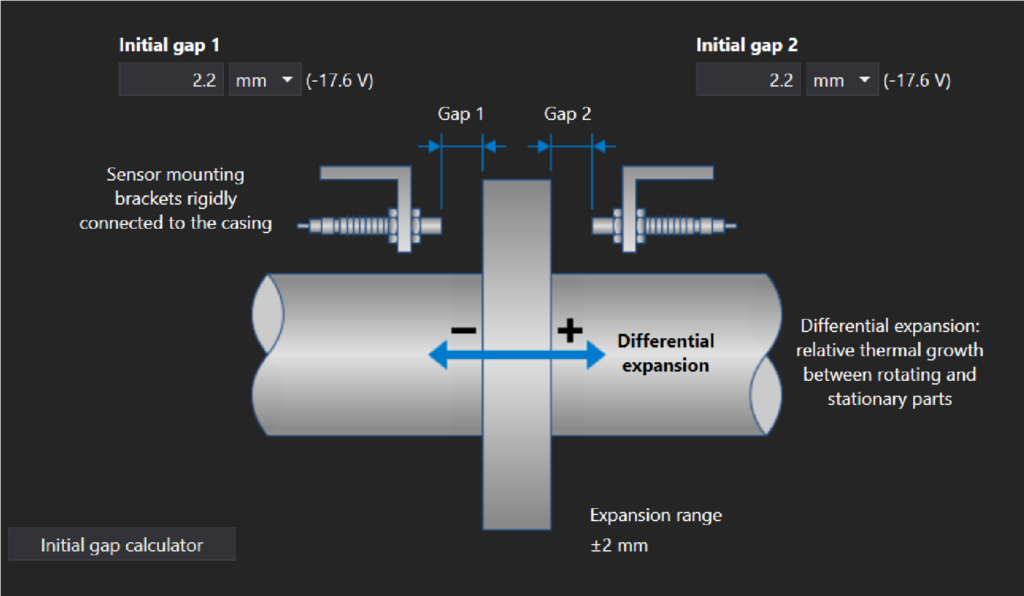
Instrumentação de supervisão de turbinas – Figura 4 – Captura de ecrã do software de configuração do VM600Mk2 (VibroSight PROTECT) que representa uma medição DCDEC.
Expansão diferencial de canal duplo (cone duplo) DCDEDT
Ao utilizar uma superfície cónica (em rampa) no veio, uma sonda radial pode observar alterações na folga à medida que o veio cresce ou encolhe. Ao contrário de uma medição de vibração radial convencional, em que a folga da sonda não se altera à medida que o veio cresce ou encolhe axialmente, a superfície cónica alterará a folga da sonda devido ao movimento axial. Uma vez que a alteração da folga da sonda está relacionada com o seno do ângulo do cone, o alcance de uma determinada sonda pode abranger uma magnitude consideravelmente maior de expansão diferencial.
Por exemplo, se o ângulo do cone for de 12°, o alcance da sonda pode abranger aproximadamente cinco vezes mais expansão diferencial do que se estivesse apenas a observar um colar DE perpendicular.
No entanto, como a folga da sonda é um composto da posição radial do eixo na folga da chumaceira e da posição axial do cone, o sinal de uma única sonda reflete ambas as contribuições. Para isolar apenas os efeitos da posição axial do cone, e não da posição radial do eixo, é utilizada uma segunda sonda, permitindo que os efeitos da posição radial do eixo sejam subtraídos das contribuições compostas das alterações axiais e radiais. A segunda sonda pode ser utilizada para observar um segundo cone ou uma parte convencional não cónica do veio.
A medição DCDEDT está representada na Figura 5. As superfícies cónicas podem ser de desenho convexo, como se mostra, ou de desenho côncavo (a chamada “borboleta”), como se mostra na inserção.
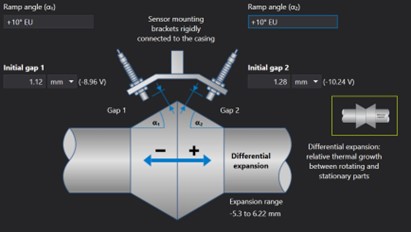
Instrumentação de supervisão de turbinas – Figura 5 Captura de ecrã do software de configuração VM600Mk2 (VibroSight PROTECT) representando uma medição DCDEDT. Neste caso, os cones estão costas com costas, formando uma forma convexa. A disposição dos cones denominada “borboleta” é mostrada na inserção verde e é utilizada por alguns fabricantes de turbinas em vez da disposição convexa, mas as considerações relativas à configuração da sonda são essencialmente idênticas.
Expansão diferencial de canal duplo (cone único) DCDEST
Esta medição é semelhante à medição DCDEDT, mas utiliza uma superfície radial convencional para uma sonda e uma superfície cónica para a outra.
As duas sondas têm o mesmo objetivo que no caso de um cone duplo, mas a sonda que observa a superfície não cónica contém apenas a informação sobre a posição radial, enquanto a sonda que observa o cone contém a informação sobre a expansão diferencial e a posição radial. No que se refere à figura 6, subtraindo o sinal da sonda 2 ao sinal da sonda 1, e através da trigonometria para a superfície cónica, é possível determinar a expansão diferencial.
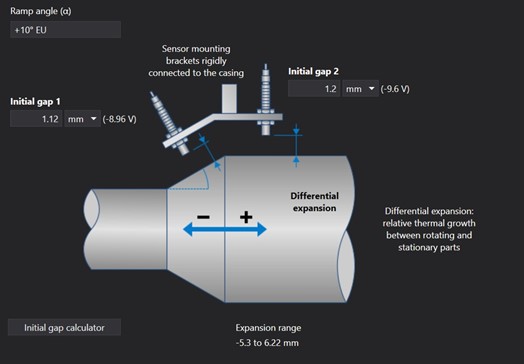
Instrumentação de supervisão de turbinas – Figura 6 Captura de ecrã do software de configuração do VM600Mk2 (VibroSight PROTECT) que representa uma medição DCDEST. Neste caso, a rampa está à esquerda.
Uma nota sobre sondas de alcance alargado
Uma das razões pelas quais são utilizadas disposições DE de canal duplo é o facto de poderem ser utilizados diâmetros de sonda mais pequenos (com intervalos lineares correspondentemente mais pequenos). Nalguns casos, contudo, são encontradas ou necessárias sondas DE com gamas lineares superiores às convencionais de 2 mm ou 4 mm. Este é frequentemente o caso das turbinas em que é utilizado um simples colar perpendicular em vez de uma superfície cónica. Para estas aplicações, são frequentemente utilizadas as chamadas sondas de “gama alargada” com diâmetros até 50 mm e gamas lineares correspondentes até 28 mm. Estas sondas podem ser tratadas pelo software de configuração do VM600Mk2 (VibroSight PROTECT) como tipos de transdutores “personalizados” e são, portanto, totalmente compatíveis com a plataforma VM600Mk2.
Expansão do corpo (HE)
Os rotores das turbinas a vapor são geralmente fixados numa chumaceira de impulso no lado interior da turbina de alta pressão e podem expandir-se a partir daí ao longo do comprimento do grupo gerador da turbina. Uma vez que a turbina de alta pressão tem o vapor mais quente, é a que sofre maior expansão e pode ser projectada para ser fixada numa extremidade da caixa, permitindo que a outra extremidade se expanda nos pés deslizantes da turbina. Se um ou mais pés ficarem presos, podem surgir problemas como uma carcaça torta (armada) ou uma carcaça presa com o resultado de um atrito entre a carcaça e o rotor e/ou uma carcaça permanentemente deformada.
A expansão da carcaça em grandes turbinas pode ser bem superior a 25-50mm e é mais frequentemente medida por meio de um LVDT (Figura 7) para monitorizar se a carcaça da turbina está a deslizar adequadamente (expandindo ou contraindo) nos seus pés.
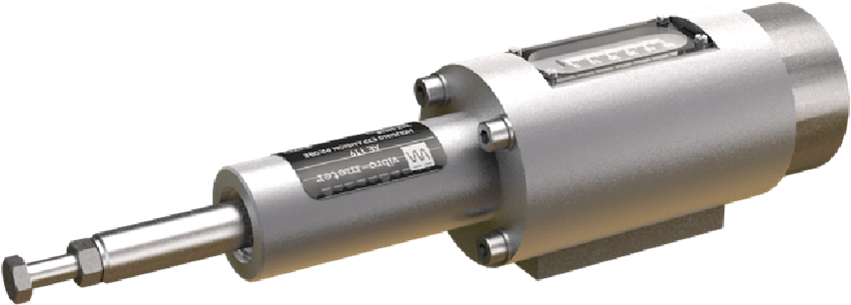
Instrumentação de supervisão de turbinas – Figura 7 O AE119 é típico dos LVDTs utilizados para medições da expansão da caixa.
As medições podem ser trazidas para o VM600Mk2 como um sinal de tensão LVDT nativo ou como um sinal variável de processo quase estático de LVDTs com uma saída de 4-20mA.
Embora seja possível utilizar um único LVDT e efetuar medições apenas num pé da caixa, é mais comum equipar ambos os lados com LVDTs, permitindo medir não só os movimentos individuais, mas também o diferencial entre os dois lados. Ver a figura 8.
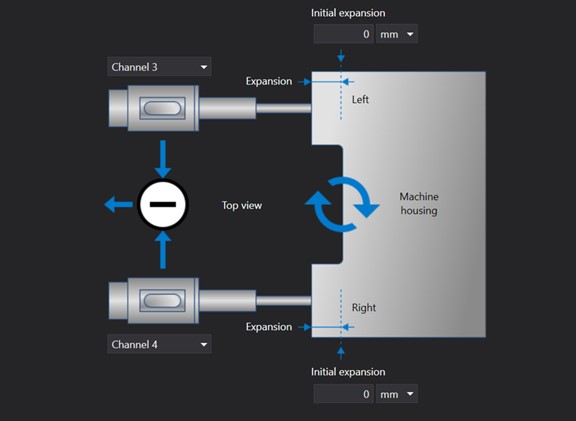
Instrumentação de supervisão de turbinas – Figura 8 Captura de tela do software de configuração VM600Mk2 (VibroSight PROTECT) mostrando uma medição de expansão da carcaça de canal duplo (diferencial). A expansão de cada lado do invólucro é medida e o monitor pode exibir esses valores absolutos, bem como o diferencial entre os dois – útil para determinar quando um único pé está preso e as chamadas condições de “invólucro armado”.
Posição da válvula VP
As válvulas de grandes dimensões são utilizadas para a admissão de vapor na turbina AP. As válvulas múltiplas são muitas vezes dispostas numa chamada “cremalheira de válvulas”, em que as cames acionam arranjos de alavancas/ êmbolos que abrem e fecham as válvulas devido ao seu tamanho substancial. A Figura 9 ilustra esta situação.
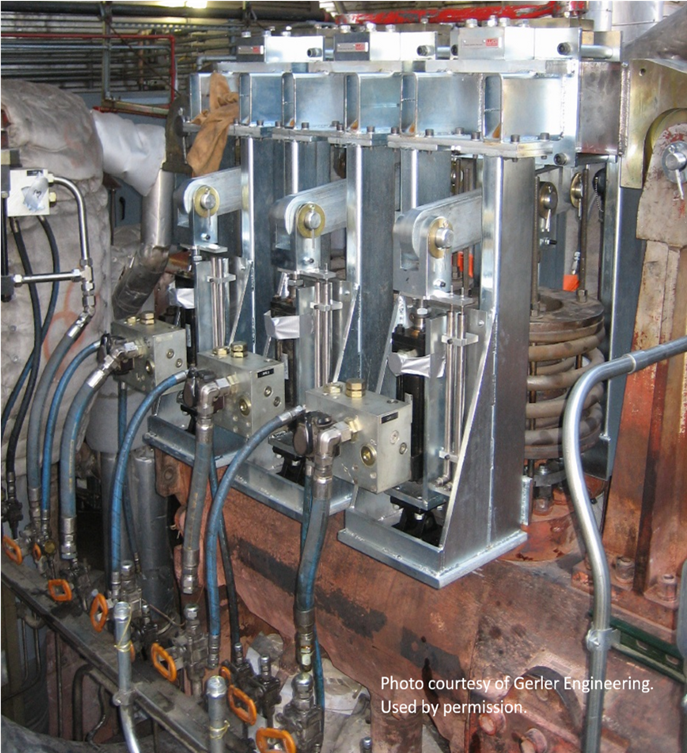
Instrumentação de supervisão de turbinas – Figura 9 Uma cremalheira de válvulas típica de uma turbina a vapor (em cima).
Um método para medir a posição da válvula é através de um potenciómetro rotativo que deteta a posição rotativa da came. Estes potenciómetros são raros e têm sobretudo um interesse histórico. Mais frequentemente, os LVDTs são utilizados para medir a posição do êmbolo da válvula (curso).
A medição da posição da válvula é assim semelhante à medição da expansão do invólucro, na qual os LVDTs são utilizados para medir o movimento linear. No entanto, as condições ambientais na cremalheira da válvula são normalmente mais agressivas, tanto em termos de temperatura como de humidade, devido ao vapor quente que passa através das válvulas.
Por esta razão, para as medições da posição das válvulas, são normalmente utilizados LVDTs AC em vez de LVDTs DC com as suas classificações de temperatura mais baixas suficientes para medições de expansão do invólucro.
No passado, as medições da posição das válvulas eram normalmente incorporadas no sistema TSI. Atualmente, no entanto, isto está a tornar-se menos comum e as medições são normalmente introduzidas diretamente no sistema de controlo da turbina.
A posição da válvula no sistema ETI é, portanto, mais frequentemente encontrada em situações de atualização em que um bastidor ETI mais antigo (como o sistema MMS da Vibrometer) está a ser substituído por um conjunto idêntico de medições numa plataforma de hardware mais recente, como o VM600Mk2. A medição é tratada como um tipo de canal quase estático no módulo MPC4Mk2 e pode ser feita em qualquer um dos seus 6 canais disponíveis. No entanto, como a posição da válvula não requer processamento de sinal dinâmico, ela é frequentemente alocada aos canais auxiliares 1 ou 2.
Excentricidade ECC
Uma vez que os rotores das turbinas a vapor são bastante compridos, se permanecerem em repouso durante muito tempo, defletem devido à gravidade. Em vez de permitir que o trem de turbina pare de girar completamente quando a turbina a vapor não está em operação, ele é geralmente colocado em uma engrenagem giratória (às vezes chamada de girador, engrenagem de elevação ou engrenagem de barramento) que gira lentamente o trem em velocidades tão baixas quanto 2-3 rpm, evitando assim o desenvolvimento de um arco flexível.
De qualquer forma, uma certa magnitude de arco estará presente nos rotores e, durante o arranque, a extensão deste arco deve ser cuidadosamente monitorizada e controlada. Esta medição é conhecida como excentricidade do rotor – ou simplesmente excentricidade – e está representada na Figura 10.
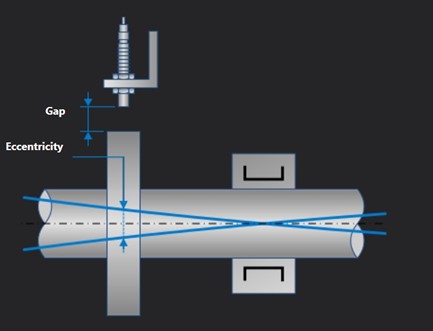
Instrumentação de supervisão de turbinas – Figura 10 Captura de ecrã do software de configuração VM600Mk2 (VibroSight PROTECT) que representa uma medição da excentricidade. Ao contrário da vibração radial, que é medida muito perto da localização de uma chumaceira, a excentricidade é medida numa localização onde qualquer curvatura residual do veio será bastante pronunciada.
As medições da excentricidade são efetuadas para garantir que a quantidade de curvatura não é excessiva, permitindo um arranque seguro dentro de limites de vibração aceitáveis. Em casos graves de curvatura, quando a máquina não foi parada devido a excentricidade excessiva, sabe-se que os operadores fletiram um rotor para além dos seus limites elásticos, resultando num veio permanentemente empenado em vez de uma curvatura temporária.
A medição da excentricidade é geralmente feita perto da carcaça da turbina de alta pressão, bem afastada axialmente de um mancal ou ponto nodal e, portanto, onde a excentricidade será mais pronunciada e facilmente observada (geralmente na extensão do tubo da turbina AP no padrão frontal). A máquina da Figura 1.1 é, portanto, típica, uma vez que a medição da excentricidade é efetuada na extremidade exterior extrema da caixa AP, como se mostra na Figura 1.2.
Velocidade zero ZS
Como mencionado na secção sobre excentricidade, o empeno do veio é uma preocupação nas grandes turbinas a vapor e, por isso, é utilizada uma engrenagem rotativa em vez de permitir que o rotor fique completamente parado quando a turbina não está a funcionar.
As engrenagens rotativas são normalmente engatadas quando o rotor abranda para uma velocidade aceitável – normalmente inferior a 100 rpm nalgumas turbinas e noutras muito mais lenta e na ordem de apenas 2-3 rpm. A estas velocidades, se for utilizado um sinal de referência de fase convencional, uma vez por volta, para indicar a velocidade, pode demorar até 30 segundos entre os impulsos medidos pela sonda indicadora de velocidade.
Por esta razão, é normalmente utilizada uma roda dentada ou uma engrenagem, o que permite atualizar a velocidade com maior frequência e medi-la com maior precisão (não é necessária uma volta completa do veio para detetar a mudança). Ver Figura 11.
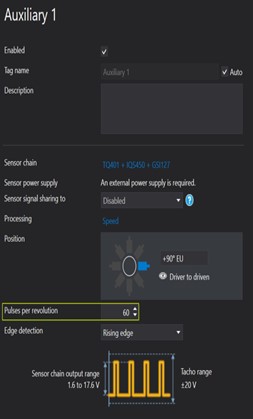
Instrumentação de supervisão de turbinas – Figura 11 Captura de ecrã do software de configuração do VM600Mk2 (VibroSight PROTECT) que representa uma medição do tacómetro de uma engrenagem de 60 dentes. Esta configuração é típica das medições de velocidade zero, em que devem estar disponíveis atualizações adequadamente rápidas – para além do que está disponível a partir de um marcador de fase uma vez por revolução quando uma máquina está a rodar a rpm muito baixas.
A medição da velocidade zero é simplesmente um alarme de velocidade insuficiente que deteta quando a velocidade de rotação desceu abaixo de um limiar aceitável e a engrenagem rotativa pode assim ser engatada em segurança. Uma vez que a medição é tão crítica e as implicações do acionamento de um mecanismo rotativo antes de o rotor ter desacelerado suficientemente são tão substanciais, é habitual utilizar sondas redundantes e comparar as medições de rpm de cada uma para garantir que estão de acordo dentro de uma percentagem configurável.
3 Instrumentação de supervisão da turbina – Medições convencionais
Todas as máquinas com chumaceiras radiais e axiais (axiais) de película fluida, são mais bem monitorizadas por um conjunto de medições que não são exclusivas dos grandes geradores de turbinas a vapor. Como tal, não podem ser corretamente designadas por medições “IST”, mas fazem parte do conjunto total de medições para estas máquinas. Estas são vistas de seguida.
Vibração relativa do veio X-Y XYSRV
Estas medições (figura 12) são efetuadas com um par de sondas de proximidade ortogonais montadas perto de cada chumaceira radial.
A disposição ortogonal das sondas permite efetuar medições em cada plano de vibração.
Dado que as direções de montagem da sonda raramente são verdadeiramente horizontais e verdadeiramente verticais, são geralmente referidas como X e Y em vez de horizontais e verticais. Não só pode ser medida a vibração em cada direção, como também pode ser obtida uma medição composta que mostra a órbita do veio.
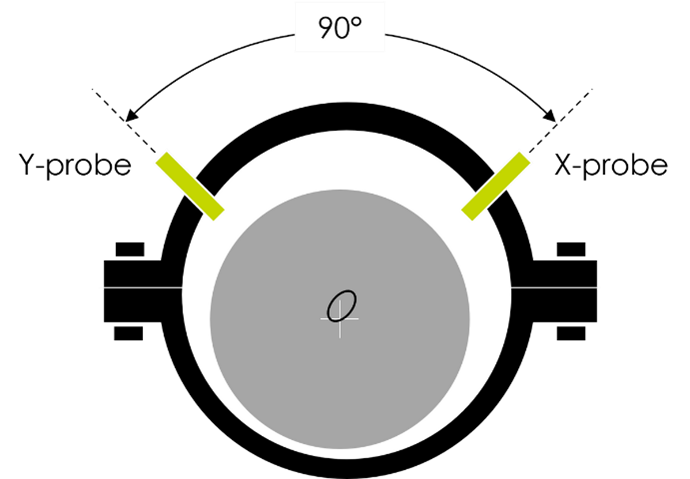
Instrumentação de supervisão de turbinas – Figura 12 – As medições das vibrações relativas ao veio X-Y são efetuadas por meio de duas sondas de proximidade ortogonais. Estas observam a posição instantânea do veio dentro da folga da chumaceira, relativamente ao local de montagem da sonda (normalmente a caixa da chumaceira).
O maior eixo da órbita é conhecido como Smax e é um parâmetro comum calculado pelo sistema de monitorização para avaliar a gravidade da vibração – particularmente nos países europeus. Ver também as figuras 13.1 e 13.2.
Quando apenas é utilizada uma única sonda, a medição é referida simplesmente como vibração relativa do veio (o X-Y é omitido). Isto é geralmente desaconselhado porque só é capaz de observar a vibração numa única direção e é, portanto, “cego” para a vibração no eixo ortogonal – independentemente da sua gravidade.
Uma única sonda também limita as capacidades de diagnóstico porque uma órbita já não pode ser gerada juntamente com a informação altamente útil que contém.
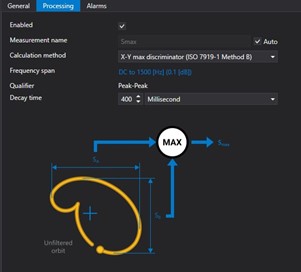
Instrumentação de supervisão de turbinas – Figure 13.1

Instrumentação de supervisão de turbinas – Figura 13.2 Capturas de ecrã do software de configuração do VM600Mk2 (VibroSight PROTECT) representando uma medição de vibração relativa ao veio X-Y. Essa configuração cria um par de canais capaz de retornar não apenas amplitudes individuais, mas também medições compostas, como Smax. Neste exemplo, a sonda X está no canal 1 e a sonda Y está no canal 2. A captura de ecrã mais abaixo mostra o sinal composto das duas sondas, resultando numa órbita do veio. O eixo maior da órbita do veio é conhecido como Smax e é frequentemente utilizado como um parâmetro de proteção.
Vibração absoluta da chumaceira / Vibração absoluta do veio BAV/SAV
As centrais térmicas empregam normalmente edifícios de vários níveis com as turbinas no último andar, permitindo que a tubagem e a admissão de vapor associada venham de baixo das turbinas. Tais projetos resultam frequentemente em estruturas de suporte conformes onde podem ocorrer vibrações sísmicas substanciais (caixa das chumaceiras).
Embora isto não se limite aos grandes geradores de turbinas a vapor, é bastante típico deles. Para tais máquinas, é aconselhável medir tanto a vibração relativa do veio X-Y, conforme referido no ponto anterior, como também a vibração da caixa da chumaceira
Embora as medições da vibração da caixa da chumaceira sejam frequentemente efetuadas no “ponto morto superior” da tampa da chumaceira e, portanto, no eixo vertical puro (Figura 14), também é possível montar sensores sísmicos (isto é, de velocidade ou aceleração) ortogonalmente no mesmo eixo que a(s) sonda(s) de proximidade relativa do veio na mesma chumaceira.
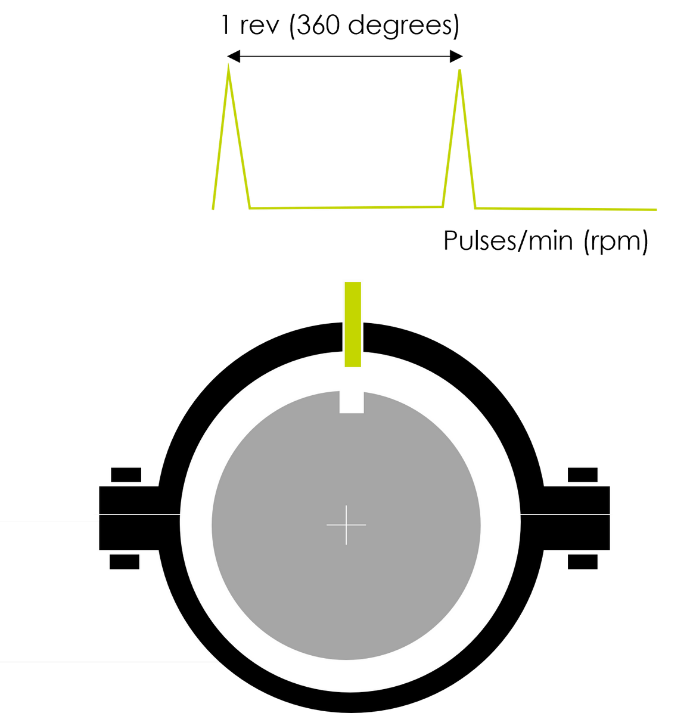
Instrumentação de supervisão de turbinas – Figura 14 – A medição da vibração absoluta da chumaceira envolve a utilização de um sensor sísmico (velocidade ou aceleração) para medir a vibração da caixa da chumaceira (ou “tampa”) em relação ao espaço livre; mede apenas o movimento da caixa – não o movimento do veio.
Nesta disposição, podem ser efectuadas as chamadas medições “absolutas do veio”, que representam a subtração do movimento sísmico da tampa do movimento relativo do veio.
Uma vez que as sondas de medição de proximidade medem o movimento relativo combinado entre a caixa da chumaceira e o veio, subtraindo o movimento da caixa da chumaceira, é possível isolar o movimento do veio em relação ao espaço livre e não em relação à caixa da chumaceira. Por este motivo, é assim descrita como uma medição absoluta do veio. Ver Figura 15.
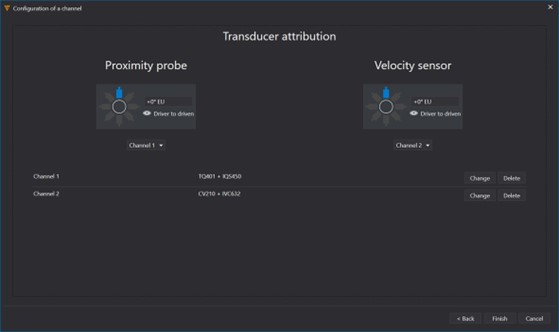
Instrumentação de supervisão de turbinas – Figura 15 – Captura de ecrã do software de configuração VM600Mk2 (VibroSight PROTECT) que mostra um par de canais utilizado para efetuar uma medição absoluta do veio. É constituído por uma sonda de proximidade no canal 1 e um sensor de velocidade no canal 2.
Posição axial (impulso) AP
As medições da posição axial (ver Figura 16) são utilizadas para determinar se as forças de impulso estão a ocorrer na direção esperada (ou seja, normal) ou numa direção anormal (ou seja, contrária) e se a chumaceira está a restringir adequadamente o movimento axial do veio.
As falhas das chumaceiras de impulso podem ser especialmente catastróficas porque permitem que as peças rotativas e estacionárias entrem em contacto ao longo de todo o comprimento do veio, danificando assim potencialmente todo o rotor e todas os estatores da máquina.
Uma vez que esta medição é de importância vital como parte da estratégia de proteção da máquina, incorpora habitualmente duas sondas numa disposição de votação dupla (2 em 2), em que ambas as sondas têm de detetar um movimento excessivo antes de emitir um alarme. Esta votação é exigida pela norma API 670 para sistemas de proteção de máquinas e é uma boa prática recomendada para todas as máquinas. Existe também uma opção de configuração para votação 1-de-2.
NOTA: Quando as sondas axiais são fixadas rigidamente à caixa da máquina, em vez de à estrutura da chumaceira de impulso, o efeito devido ao movimento da estrutura da chumaceira é eliminado da medição. Isto é conhecido como posição do rotor, uma vez que indica a quantidade de movimento relativamente à caixa da máquina e não relativamente à chumaceira à qual está ligada (e que também se pode mover). Ao contrário das medições do rotor em carcaças que sofrem uma expansão térmica significativa, a medição da posição do rotor é assumida como sendo em carcaças que exibem uma expansão térmica insignificante. Quando a própria caixa pode sofrer uma expansão/contração térmica, a sonda deve ser fixada na fundação da máquina e não na sua caixa.
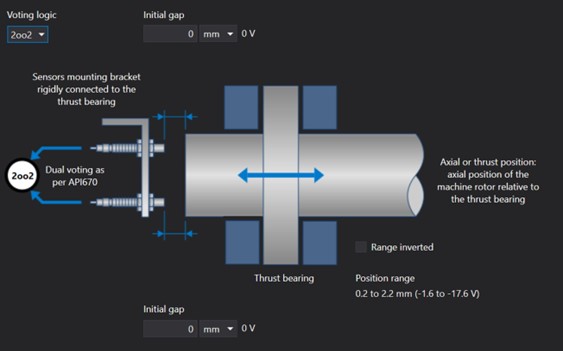
Instrumentação de supervisão de turbinas – Figura 16 Captura de tela do software de configuração VM600Mk2 (VibroSight PROTECT) mostrando uma medição de posição axial de votação dupla (2oo2). A votação 1oo2 é também uma opção configurável, utilizando a seleção da lógica de votação adequada no canto superior esquerdo do ecrã.
Disparador de fase PT
Semelhante a uma marca de temporização na cambota de um motor automóvel, um sensor de disparo de fase fornece um impulso de referência que permite determinar a posição de rotação (graus de rotação) do veio num instante preciso.
Esta medição permite calcular a fase de vibração para todas as sondas de vibração radial e sensores de tampa da chumaceira, bem como medições filtradas para múltiplos da velocidade de funcionamento da máquina, tais como 1X, 2X, ½X, etc.
A fase é muito útil para o diagnóstico de vibrações e é, de facto, tão útil que o diagnóstico é muito prejudicado se esta informação de referência de fase se perder. Por esta razão, muitos utilizadores preferem instalar sondas de disparo de fase redundantes para que, no caso de a sonda primária falhar, a secundária esteja disponível.
Ao contrário de muitas outras medições, tais como um sensor de vibração radial avariado, um sensor de disparo de fase avariado afeta quase todos os outros sensores em termos de capacidades de diagnóstico de máquinas disponíveis. A descontinuidade da superfície do veio para um disparador de fase é frequentemente uma chaveta (projeção) ou um rasgo de chaveta (entalhe), mas por vezes consiste numa ranhura feita especificamente para este fim.
Nos grandes geradores de turbinas a vapor, deve ter-se o cuidado de colocar a marca num local onde o crescimento térmico do rotor não faça com que a descontinuidade se desloque para fora do campo observável da sonda, como pode acontecer quando a medição ocorre na extremidade extrema do veio, perto do gerador ou do excitador.
Se não houver outra localização adequada, a descontinuidade deve ser suficientemente longa para que qualquer expansão ou contração não permita que a descontinuidade saia do campo observável da sonda.
Um sensor de disparo de fase pode também ser utilizado para medições de velocidade, mas a taxa de atualização e a precisão não serão tão boas como as obtidas com uma roda de dentes múltiplos, como a utilizada para a medição da velocidade zero. No entanto, isto não é normalmente uma preocupação para as máquinas que rodam a velocidades médias, como uma turbina a vapor de 3000 rpm ou 3600 rpm que aciona um gerador.
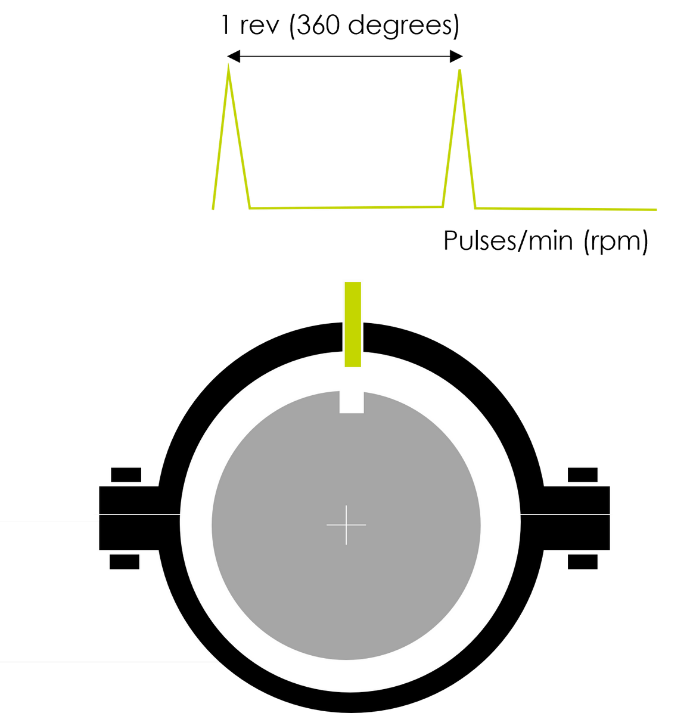
Instrumentação de supervisão de turbinas – Figura 17 Um sensor de disparo de fase (ou de referência de fase) fornece um sinal de uma vez por volta utilizado para medições de fase.
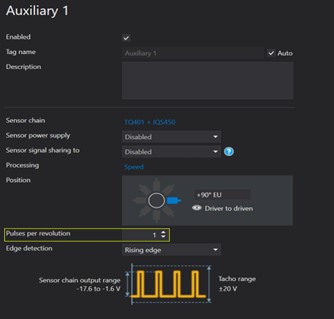
Figura 18 Captura de ecrã do software de configuração do VM600Mk2 (VibroSight PROTECT) que mostra uma medição de referência de fase. Ao contrário da configuração da Figura 11 (60 impulsos por rotação), um verdadeiro disparador de fase deve ter apenas um único impulso por rotação.
Temperatura da chumaceira T
A carga excessiva em chumaceiras de película fluida – radial ou axial – pode derreter o material babbitt e causar grandes problemas para além da chumaceira, se não for detetada.
É habitual incorporar sensores de temperatura – RTDs ou termopares – na chumaceira para medir as temperaturas das almofadas e garantir que estas se mantêm dentro de limites aceitáveis, bem abaixo do ponto de fusão do babbitt.
Atualmente, as medições de temperatura são frequentemente efetuadas diretamente no sistema de controlo da turbina, onde também podem residir outros parâmetros de proteção.
No entanto, muitos utilizadores ainda preferem colocar estas medições no sistema de monitorização de vibrações. Para estes, o VM600Mk2 pode aceitar diretamente tanto termopares como RTDs através de módulos especiais de monitorização de 8 canais.
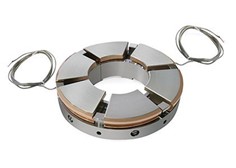
Figura 19 Uma típica chumaceira axial de almofada basculante com dois sensores de temperatura incorporados.
Sobrevelocidade
O excesso de velocidade de uma turbina é um dos cenários mais potencialmente catastróficos que uma máquina pode suportar. Uma vez que as forças centrípetas que atuam sobre as peças rotativas, como as pás e os acoplamentos da turbina, estão relacionadas com o quadrado da velocidade de rotação, uma turbina é concebida para suportar apenas pequenas excursões (20-30%) para além da sua velocidade nominal – quer seja concebida para 50 Hz (3000 rpm) ou 60 Hz (3600 rpm).
Quando ocorrem forças centrípetas excessivas, as pás podem libertar-se do rotor, tornando-se projéteis e podendo perfurar a caixa. Além disso, os rotores podem dobrar-se, os acoplamentos podem soltar-se e a máquina pode literalmente “explodir” (Figura 20).
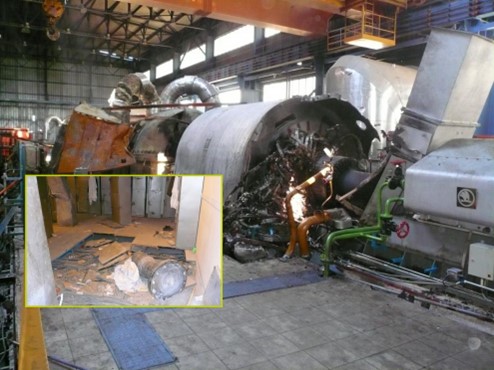
Figura 20: Consequências do excesso de velocidade catastrófico de um gerador de turbina a vapor de 64 MW. Uma porção maciça de uma peça da bobina do veio (inset) perfurou uma parede a muitos metros de distância durante o evento, vindo a parar no balneário dos homens.
No caso de uma turbina a vapor, isto pode ser especialmente consequente, porque o vapor quente e de alta pressão já não está confinado dentro do recipiente sob pressão (caixa da máquina) e pode infligir danos tremendos a pessoas e bens quando se escapa.
Por todas estas razões, as medições de excesso de velocidade são muito especializadas, envolvendo várias camadas de tacómetros e sensores redundantes, muitas vezes numa disposição de 2 em 3 para atingir o nível SIL 3.
Os canais do tacómetro da plataforma VM600Mk2 não se destinam, portanto, a medições de excesso de velocidade. Em vez disso, existe a plataforma SpeedSys300 (Figura 21), especificamente concebida para aplicações de velocidade excessiva de turbinas.
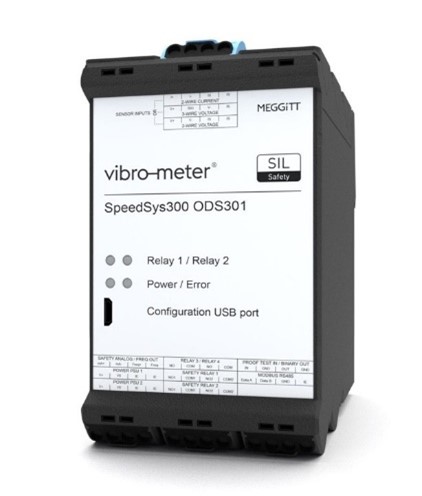
Figura 21 – O SpeedSys 300 da Vibro-meter é um sistema de deteção de excesso de velocidade com classificação SIL 3.
A melhor prática da indústria consiste em separar o sistema de excesso de velocidade do sistema de controlo da turbina, bem como do sistema de vibração da máquina. O SpeedSys300 foi assim concebido como uma plataforma autónoma para a proteção do excesso de velocidade.
3 Resumo da instrumentação de supervisão da turbina
O VM600Mk2 foi especialmente projetado para atender às necessidades de medição da maioria dos tipos de máquinas industriais, incluindo turbinas a gás e a vapor. Para turbinas a vapor em serviço de geração de energia, são necessárias medições especializadas de TSI e o VM600Mk2 tem tipos de canais para atender a cada uma delas. Como o VM600Mk2 usa um projeto inovador de “módulo único” para fornecer todos os tipos de canais num único módulo (MPC4Mk2), as peças de reserva são drasticamente reduzidas.
Para além das funções de proteção da máquina, o novo MPC4Mk2 incorpora capacidades integradas de monitorização da condição, fornecendo todas as funcionalidades necessárias de medições na máquina num projeto compacto de 6 canais que ocupa apenas uma única ranhura no chassis do VM600.
Os utilizadores podem, assim, confiar na Vibrometer para responder plenamente às necessidades destas importantes máquinas com uma plataforma de segunda geração que fornecerá uma proteção fiável e uma monitorização da condição durante as próximas décadas.
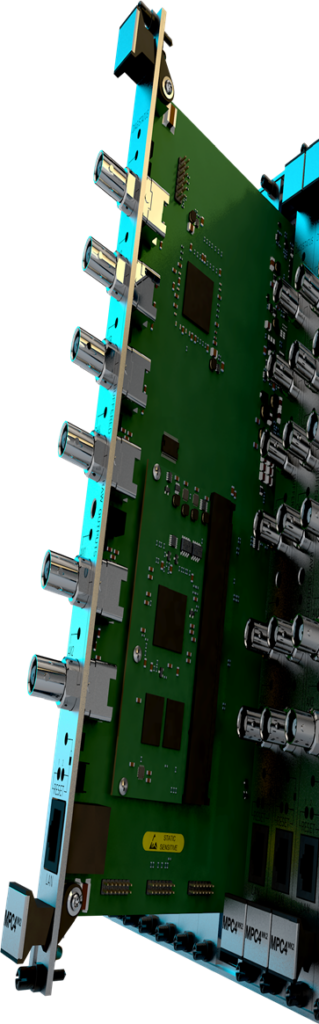