Turbomachinery and Full Spectrum
An important measurement made with the Vibration analyzers is the one of turbomachinery starts and stops and full spectrum.
This article belongs to a series, which constitutes the support material for the course on vibration analysis in turbomachinery. Links to the other articles can be found on here.
the conventional spectrum
the conventional spectrum, or half spectrum, displays the amplitude of vibration on the vertical axis versus the frequency of vibration on the horizontal axis. It is constructed using the time base waveform sampled from a single transducer.
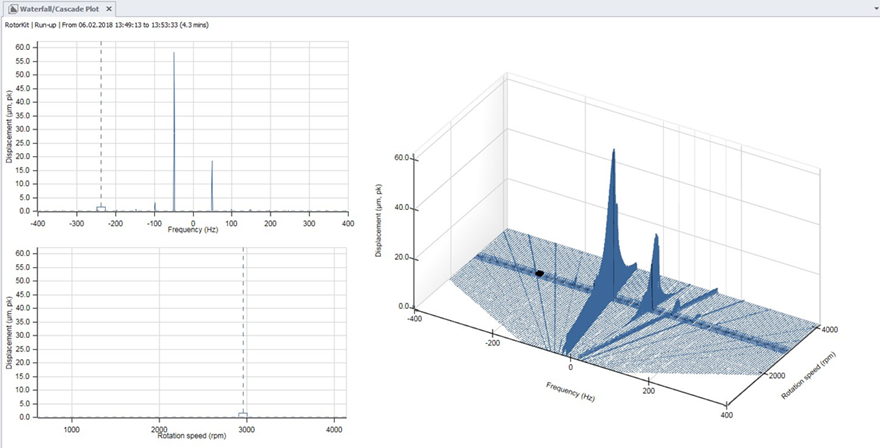
Turbomachinery and Full Spectrum – Figure 1 – Conventional spectrum and full spectrum
Turbomachinery and Full Spectrum – yours training
Full spectrum uses waveforms from an orthogonal pair of vibration transducers (usually relative to the shaft). The full spectrum shows the frequency and direction of precession on the horizontal axis.
- The precession frequencies direct are displayed to the right of the origin
- The precession frequencies reverse are displayed to the left of the origin.
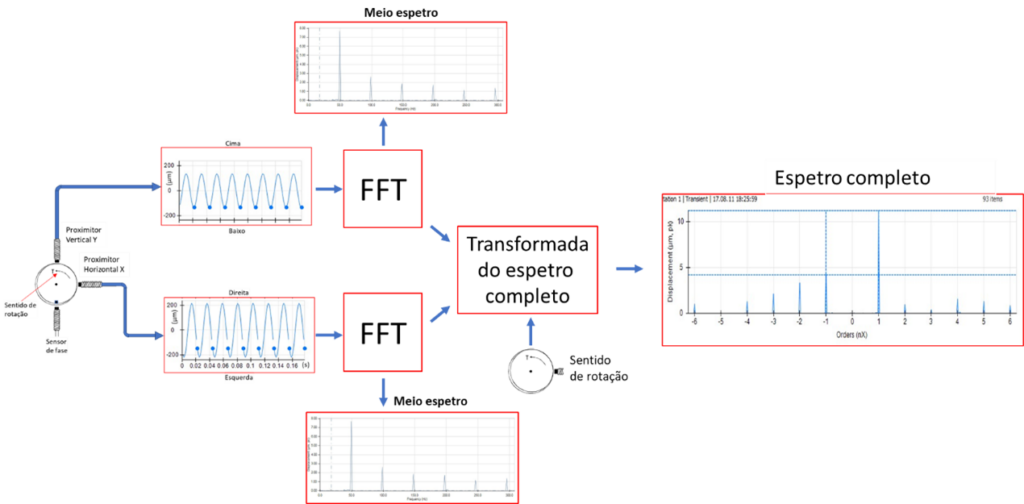
Turbomachinery and Full Spectrum – Figure 2 – The formation of the Full Spectrum
The full spectrum is the spectrum of an orbit, and the pairs of forward and reverse frequency components represent orbit components (filtered orbits). The ratio of amplitudes of pairs of full spectrum components provides information about the ellipticity and precession direction of the components, important features for troubleshooting. However, there is no information about the orientation of the orbit.
Relationship between the orbit and the Full Spectrum.
In the following video you can see the relationship between the orbit and the full spectrum.
Full Spectrum Applications
In the table below you can see how the symptoms of different anomalies appear in the full spectrum.
Table 1 – Symptoms of various full-spectrum anomalies
type of failure | Frequency | direction of rotation | comments | ||
direct | reverse | ||||
Imbalance | 1X | + | In the presence of anisotropic support stiffness | The direct component is fundamental for the balance. The inverse component can be reduced by reducing the anterior component.. | |
radial unidirectional force | 1X | + | + | With increasing radial load, the direct components at 1X and 2X decrease, the inverse components at 1X and 2X increase; the ellipticity of the 1X and 2X orbits increases. | |
2X | + | + | |||
partial friction | 1X | + | + | The 1X and 2X components behave similarly to the unidirectional radial load: increase in the amplitude of the inverse component and decrease in the amplitude of the direct component with increasing severity of friction. One thing to look out for is the rotation of the main axis of the filtered orbit. The 1/2X components, 1/3X, … appear if the rotation speed is greater than, correspondingly, 2, 3, … times the friction-modified natural frequency of the rotor. These subsynchronous frequencies have forward and backward components.. Corresponding filtered orbits are too elliptical, and the inverse components may be predominant. | |
2X | + | + | |||
1/2X, 1/3X, …. | + | + | |||
complete annular friction | forced answer | 1X | + | – | Depending on dry friction between impeller and seal, the susceptibility of the sealant, damping and imbalance, the system may display a forced response, predominantly 1X forward, or a self-excited response, predominantly inverse. |
self excited response | Natural frequency of the rotor-sealant coupler system | – | + | ||
Oil whirl | λX λ=0.3 to 0.6 | + | – | Predominantly direct orbit with internal loops (a combination of tourbillon and 1X components). Reflects across the spectrum as a direct subsynchronous component. | |
Oil whip | Excitation of the natural frequency of the rotor | + | + | Predominantly direct orbit with internal loops (a combination of whip and 1X components). Normally, some inverse 1X and subsynchronous components are present due to anisotropy of bearing pedestal stiffness. |