Vibration monitoring in TOP10
This article is about Vibration Monitoring, no TOP10, permanently, of the biggest turbo machines, sorted by power, in Portugal.
This article belongs to a series, which constitutes the support material for the course on vibration analysis in turbomachinery. Links to the other articles can be found on here.
The TOP10, of the biggest turbo machines, sorted by power, in Portugal.
Below you can see, in ascending order, the centers and characteristics of the various groups in the TOP10.
10 – Bemposta II Dam | ||
![]() | Place not TOP10 | 10 |
group type | water | |
Number of groups | 1 | |
group poop power (MW) | 191 |
9 – Gouvães dam | ||
![]() | Place not TOP10 | 9 |
group type | water | |
Number of groups | 4 | |
group poop power (MW) | 220 |
8 – Home Center | ||
![]() | Place not TOP10 | 9 |
group type | Gas | |
Number of groups | 2 | |
group poop power (MW) | 221 |
7 – Picote II dam | ||
![]() | Place not TOP10 | 7 |
group type | water | |
Number of groups | 1 | |
group poop power (MW) | 246 |
6 – Alqueva dam | ||
![]() | Place not TOP10 | 6 |
group type | water | |
Number of groups | 2 | |
group poop power (MW) | 260 |
5 – Alto-Lindoso dam | ||
![]() | Place not TOP10 | 5 |
group type | water | |
Number of groups | 2 | |
group poop power (MW) | 315 |
4 – Tapada do Outeiro Central | ||
![]() | Place not TOP10 | 4 |
group type | Gas | |
Number of groups | 3 | |
group poop power (MW) | 330 |
3 – Venda Nova III dam | ||
![]() | Place not TOP10 | 3 |
group type | water | |
Number of groups | 2 | |
group poop power (MW) | 373 |
2 – Charge Center | ||
![]() | Place not TOP10 | 2 |
group type | Gas | |
Number of groups | 3 | |
group poop power (MW) | 330 |
1 – Central do Pego | ||
![]() | Place not TOP10 | 1 |
group type | Gas | |
Number of groups | 3 | |
group poop power (MW) | 330 |
Permanent monitoring systems for vibrations in turbo machines in the TOP10
Below you can see a table with the permanent vibration monitoring systems in the turbo machines in the TOP10, in Portugal.
Place not TOP10 | Central | group type | No. of groups | Power of each group (MW) | monitoring system |
1 | Caught | Gas | 2 | 418 | Vibrometer VM600 |
2 | Loaded | Gas | 3 | 392 | Vibrometer VM600 |
3 | Venda Nova III dam | water | 2 | 373 | |
4 | Tapada do Outeiro | Gas | 3 | 330 | Vibrometer VM600 |
5 | Alto-Lindoso dam | water | 2 | 315 | |
6 | Alqueva dam | water | 2 | 260 | Vibrometer VM600 |
7 | Picote II dam | water | 1 | 246 | Vibrometer VM600 |
8 | homes | Gas | 2 | 221 | |
9 | Gouvães | water | 4 | 220 | |
10 | Bemposta II | water | 1 | 191 | Vibrometer VM600 |
Total | 22 | Total 12 Vibrometer VM600 |
In the previous table it can be seen that more than half of the machines in the TOP10, i.e. 12, is monitored with the Vibrometer VM600 system.
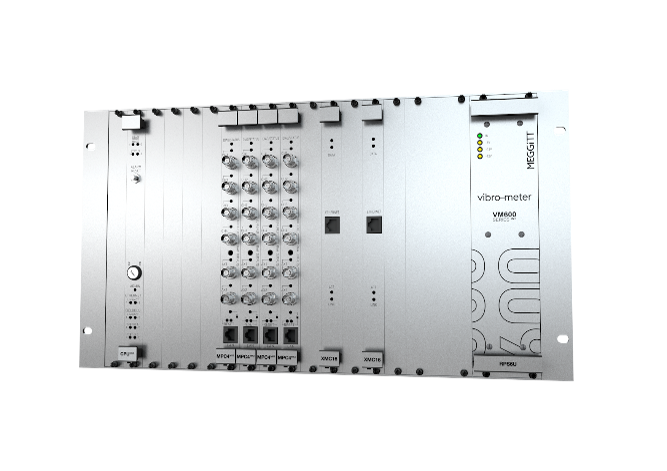
Because permanent monitoring of vibrations in turbomachinery?
Manufacturers of this type of machine supply them with these systems already installed.. This is so because mathematical models of reliability and experience, showed that, to achieve the availability and reliability goals that their customers expect from them, these systems are indispensable.
Large turbo machines, are usually very reliable, but taking into account the costs of unavailability and associated with unforeseen breakdowns, permanent protective monitoring systems, are essential to achieving your economic goals.
Characteristics of a permanent monitoring system for vibrations in turbomachinery
A permanent monitoring system for vibrations in turbomachinery, like the VM600, usually has two functions:
- Machine protection from excessive vibrations (SPM);
- Provide information about its operating condition (CMS).
In 1970, the American Petroleum Institute defined the proximity probe as the measuring device for measuring acceptable shaft vibration, during factory acceptance tests. This was added as a requirement in their standard for centrifugal compressors.. The eddy current proximity probe has become the preferred method for assessing vibration and general mechanical condition in big turbomachines that employ oil film bearings. Such machines and types of bearings are responsible for the vast majority of compressors., turbines, bombs, electric motors, generators and other rotating equipment greater than 1.000 HP, and can be found in abundance..
This standard, O API 670, became the de facto standard for monitoring vibrations in turbomachinery and is now widely used in industry..
Independence and separation of systems, components or parts is an important design concept underlying the entire standard. For example:
- A segregation (4.8) requires that the Machine Protection System (SPM) be totally separate from any other systems, like another protection system, control systems or Condition Monitoring Systems (CMS).
- Within the SPM, all machine protection loops are normally wired (wireless communication is not allowed here) and the interconnections with other devices in the machine's automatic stop loop, are implemented through system output relays (4.12).
- A problem with a measurement chain, input channel or signal processing should not affect any other channel. This applies to system power supplies (4.10), as well as the power supplies of individual sensors. To mitigate these failures, SPMs often use redundant power supplies (11).
- You digital communication links (4.13) for systems outside the SPM, as a CMS, must not affect the protective functions of the machines. This also applies to buffered analog outputs (“raw”), even in the event of a short circuit at these outputs.
- Similarly, a interchangeability (4.6) implies that it must be possible to physically and electrically replace the components of the SPM in-situ, without leaving the measurement accuracy requirements.
Why the Meggitt VM600 – Vibrometer?
Meggitt PLC is a global engineering group, based in the UK, specializing in the design and manufacture of high-performance components and systems for the aerospace and energy markets.
The Meggitt facility in Fribourg, Switzerland, operates as the legal entity, Meggitt SA, that designs and manufactures complete condition monitoring and vibration monitoring and measurement solutions.
VIBRO-METER® is a Meggitt product portfolio that applies leading detection and monitoring technologies to power generation, oil and gas and other industrial markets.
By 70 years, VIBRO-METER® products and experience have enabled superior solutions for vibration detection and monitoring, pressure and air gap in critical installations and equipment. The comprehensive, high-quality range of sensors and measurement chains, VM600 rack-based systems, VibroSmart® and VibroSight® systems and much more, offers total solutions to monitor and protect your critical machines and processes.
Provides the best solutions for measurement and monitoring needs to project investments. This allows you to achieve higher levels of reliability., machine availability and production. Today, products are trusted by OEMs around the world and have been qualified and adopted as standard fit components in machines used in the power industry.
MEGGITT VIBRO-METER® integrated systems are chosen to monitor thousands of rotating machines worldwide, including:
- The biggest steam turbine (1800 MW)
- The most powerful gas turbine (530 MW)
- The three largest hydroelectric facilities.
Aerospace detection and monitoring systems are used by leading aerospace manufacturers and operators around the world.
Our detection capabilities are widely used in the space industry thanks to their high reliability in extreme conditions..