PREDICTIVE MAINTENANCE – GENERALITIES
1 – PREDICTIVE MAINTENANCE – GENERALITIES
predictive maintenance , in general, is the theme covered in this article..
The simplest way to operate machines is to let them work until they stop due to breakdown and then repair them so that they are fit for a new period of service.. This practice can become very expensive in terms of production losses and maintenance costs., in addition to jeopardizing the safety of people and the environment..
It is now generally accepted that, in the case of units with large capital investments, is more satisfying from an economic point of view, implement regular maintenance actions. Are, involve overhauling machines or their components at regular intervals, in order to reduce the probability of malfunctions occurring during the period in which the equipment is available. The main problem to overcome in implementing this type of maintenance, lies in choosing the appropriate time interval, between reviews. effectively, the interval at which maintenance action becomes essential is not constant, varying from one occasion to another, due to differences in service conditions and component behavior.
The figure shows the behavior of a group of machines “typical” if preventive maintenance is not carried out. In other words, the typical pattern of failure occurrence, in Curative Maintenance.
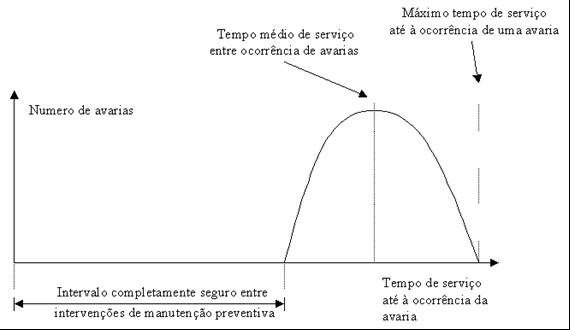
It can be seen that there is a safe time interval, between reviews, in order to avoid all breakdowns before they can occur. Yet, if you choose this interval, interventions will take place long before they are actually needed. will exist, therefore, many cases where machines could work longer without a breakdown. This practice wastes service time and by increasing the frequency of interventions, increases the incidence of human error in assemblies.
A more satisfying approach, in economic terms, is to perform preventive maintenance, at intervals that can be irregular, making interventions depend on the operating condition of the machines. To carry out this maintenance “under condition”, also called "Predictive Maintenance", It is essential to know the operating status of the equipment and its evolution over time. To do this, it is necessary to have a condition control system that provides this knowledge..
This approach considers each machine individually. Replacing revisions at fixed intervals, by inspections at fixed intervals, the evolution in the operating condition of each machine can be closely followed..
The basic axiom of Predictive Maintenance is that machines are only intervened when the inspection results show that this is necessary.. This is also in keeping with the sensitivity of most people that it is unwise to tamper with well-functioning machines..
For example, with regular measurement of the vibration levels of a pump, the symptoms of malfunctions can be detected and their development followed.. The measurement results can be extrapolated in order to predict when unacceptable levels will be reached and, therefore, when should intervene, as shown in the figure below..

2 – ADVANTAGES OF PREDICTIVE MAINTENANCE
2.1 – Economic Advantages of Predictive Maintenance
The economic advantages of Predictive Maintenance generally appear as follows:
- 2/3 of the gains from the reduction of production losses
- 1/3 gains from reduced maintenance costs
These proportions correspond to:
- Reduction of production losses corresponding to 75% of days lost annually when Predictive maintenance is not used
- Reduction in 5% of the total maintenance cost
The reason you can only wait 75% of reduction of production losses, is that some types of malfunctions, regardless of being detected, require production to be stopped. On the other hand, the condition control cannot be expected to be 100% efficient.
The number of 5% for maintenance cost reduction arises from the fact that most of the savings are in curative maintenance labor cost. Since the cost of curative repair is generally around 1/3 the total cost of maintenance and these, 1/3 be labor costs, the cost of labor in curative maintenance is about 10% do total. A halving gives the number of 5%.
In the following figure, the different types of industry are ordered., in ascending order of susceptibility, of there being gains with Predictive Maintenance. (results of a study carried out in Great Britain in 1978)

Below are some examples of predictive maintenance application.
Example 1 – Process Industry / Refinery
The figure below shows the number of stops due to problems in rotating machines in a refinery.
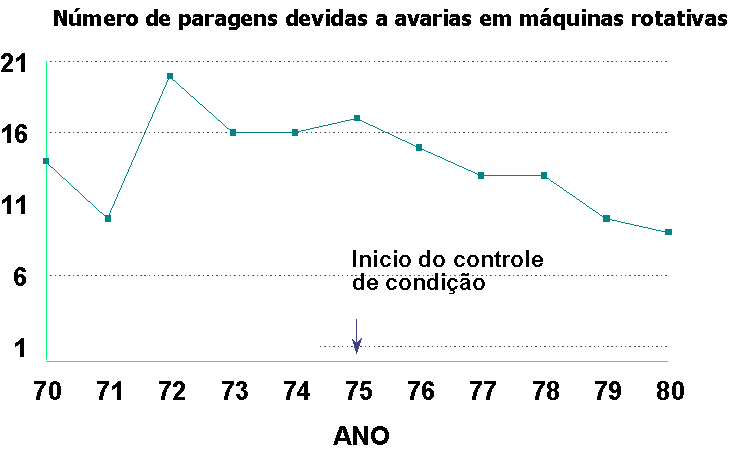
In the figure below, you can see the average number of hours needed to start after due to rotating machinery in a refinery.
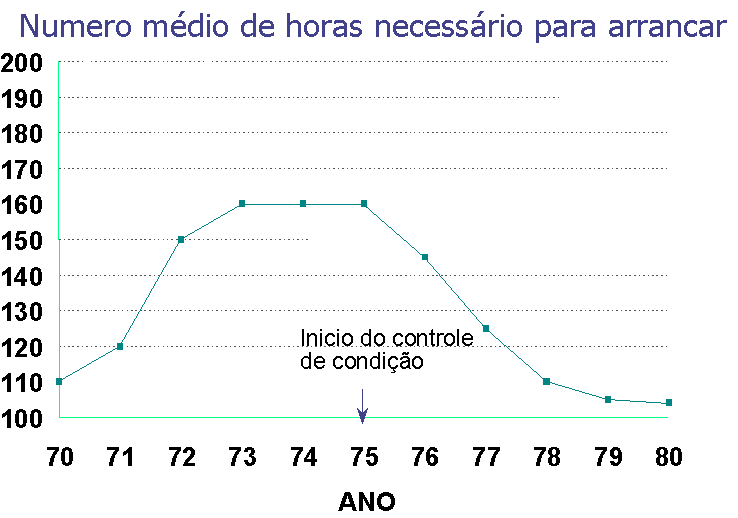
Example 2 – Electric Motor Repair Workshop
The figure below shows the failure rate in electric motor tests after revision. In 1978 an engine acceptance program was implemented after the overhaul..
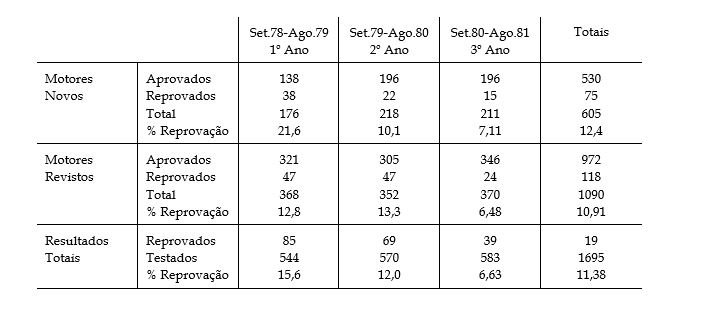
Note the sharp drop in the number of engines in poor condition, over the years.
1978 | 1981 | |
Electric motors Folks Overtime Cost of labor per year External contracts per year | 1171 7 20% $ 462 000 $ 1 272 000 | 2300 3 negligible $ 150 000 $ 860 000 |
Example 3 – Maintenance Cost per Horse per Year – Power generation
The figure below shows the maintenance cost per horse per year in the power generation industry.

Example 4 – Stops due to malfunctions in rotating machinery, on two paper machines
The figure below shows the number of stops due to malfunctions in rotary machines on two paper machines, before and after starting a predictive maintenance program.
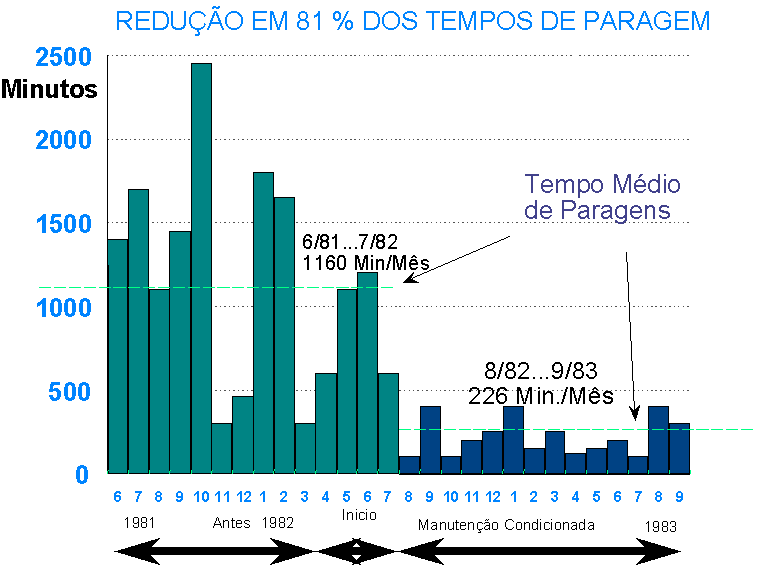
2.2 – Other Advantages of Predictive Maintenance
Economic advantages are not the only valid point of view to consider when implementing it., or not, a Condition Control system. Since there are different kinds of advantages, in each specific case there will be factors that are particularly favorable or unfavorable for Predictive Maintenance.
These are listed in the tables below..
QUADRO I
Controlling the condition of machines can provide the following benefits | way the benefits appear |
1) Increased machine operator safety | The warning time given by the condition control allows to stop the machines before reaching a critical state, especially if they can't stop instantly |
2) Increase equipment availability resulting in greater production from invested capital 3) Reduce maintenance costs | Machine service time can be increased by maximizing time between overhauls. The review duration can be shortened because the nature of the problem is known., spares and personnel are available.. Damage resulting from malfunctions can be reduced or eliminated. |
4) Greater efficiency in the conduct of facilities, allowing adjust the volume of production to the conditions of facilities, and achieve a stable quality level | The load and speed of some machines can be varied to obtain a good compromise between production and service time until the next improvement. |
5) Greater capacity for dialogue with manufacturers of machinery and equipment or repairing, based on knowledge obtained from the control condition | The inspection of new equipment, at end of warranty and after overhaul provides useful basis for comparison |
6) Better relationships with customers due to the reduction of unplanned production stoppages | Warning time before breakdown, obtained through information provided by inspections., allow this to happen |
7) Possibility to improve the specification and design of future installations | The history obtained through the inspections can be used for this purpose. |
Favorable factors for the application, successful predictive maintenance, in a factory, machine or equipment.
QUADRO II
Where there is a safety risk associated with a machine malfunction | Typical examples are factories that work with hazardous products and means of transporting people |
Where rigorous maintenance planning is required | Typical examples are equipment in remote locations only occasionally visited for maintenance, or mobile equipment that makes only occasional visits to its support base |
Where the factory or equipment is a new project where some development problems still remain | The inspection makes it possible to detect malfunctions at the beginning, while damage is slight, so that important information is available to guide improvements to the project |
Where high cost machines, subject to risk of major damage, are operated by untrained personnel or remotely | Condition control allows you to detect the problem with sufficient warning time to issue instructions to take the equipment out of service., before serious damage occurs |
Where the equipment manufacturer is able to offer a condition control service to various users of the equipment | The cost for each user can thus be reduced., and the manufacturer receives important feedback to direct the design and development of their product |
Where the instrumentation or other equipment required for the inspection is, or is already being, used for another purpose | Another application of instrumentation or equipment can be process control or other activities such as balancing or diagnostics |
3 – FAILURE FACTORS
Factors that are unfavorable to the successful application of Predictive Maintenance, to a factory, machine or equipment.
QUADRO III
Where the industry is lightly loaded and the factory or machine is frequently stopped | If the factory is frequently stopped, there are generally many opportunities for inspection and maintenance during downtime. |
Where the group of similar machines is too small to allow the accumulation of experience necessary for the effective interpretation of readings and correct decision-making on their meaning | To accumulate experience in a reasonable period of time, the minimum number usually varies between 4 a 10 depending on the type of machine or component. The problem can be solved by sharing inspection services with other factories., involving machine manufacturers or external services |
Where highly skilled operators have close contact with their machines, and can use their senses to work out a subjective bias | Machine tools and ships can be an example of this situation, but any step towards using less qualified operators, favors the application of Predictive maintenance |
Where interventions on mobile machinery or equipment are carried out in some centers where specialized labor is installed | The main function of condition control in these circumstances is to determine priorities for interventions in the different units.. Predictive maintenance in this case, has a reduced economic effect, unless it can result in project improvement or increased yield, and thus result in a reduction in the frequency of interventions and costs |
4 – CONDITION CONTROL
There are basically two methods to carry out the condition control.:
- Trend Monitoring;
- Check the working condition
Trend monitoring consists of periodic or continuous measurement, of a parameter indicating variations in the operating condition of the machine or its components. IS, therefore, evident, that it is necessary to proceed with the selection of significant indicators of deterioration of the machine or components, as are some indicated on the next page.
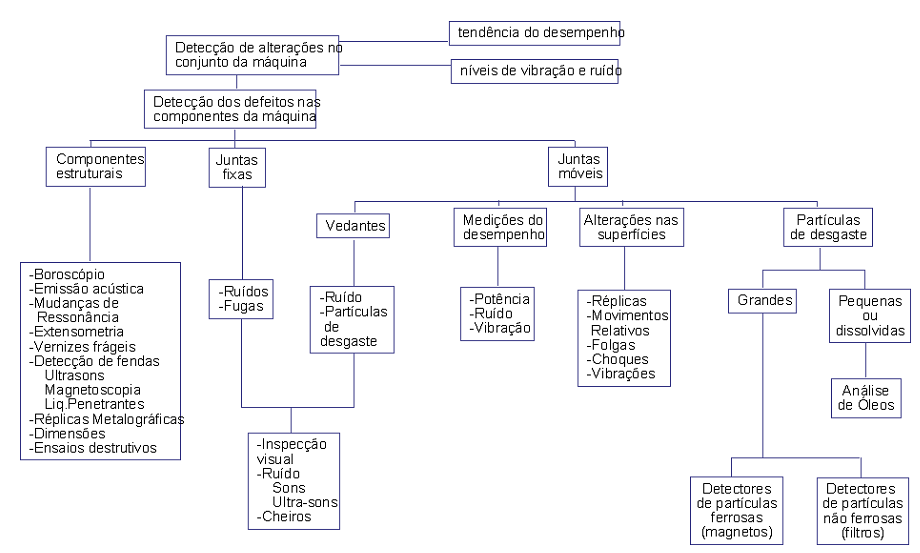
Based on the measured values, prepares a tendency for determining when the degradation of a machine exceeds a critical state, as shown in the picture.
The principles involved are illustrated in the following figure., which shows the means by which trend tracking can give a warning time before deterioration reaches a level at which the machine has to be taken out of service.

The warning time before failure occurs, is one of the main advantages of using trend tracking instead of alarms or protection relays..
Checking the condition, takes place through the measurement of a parameter, at a certain time, thereby inferring the state machine. To be effective, the measurement has to be accurate, measured values must also be known limits not to be exceeded for more than a certain number of operating hours. The limits, to be established, require a wide previous experience with the particular type of machine in question. A check of the condition is, therefore, less flexible than the trend-following, especially with regard to the warning time before failure.
It might be, However, very useful in situations where there are several machines working together, seen in this case, comparisons can be made between machines in service and machines that are new or known to be in good condition.
These two condition control methods are compared in more detail in the table below..
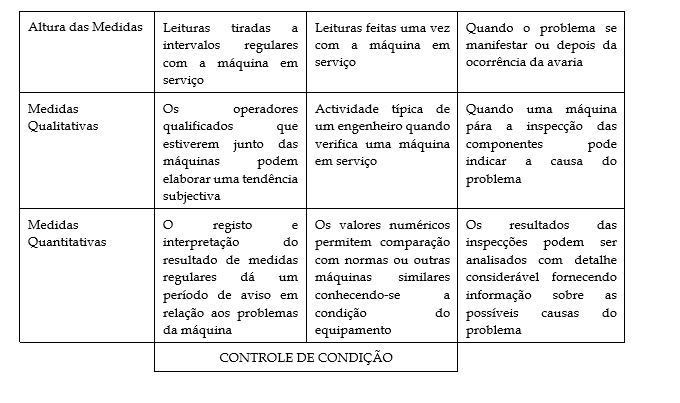
5 – THE FAULTS
in its simplest form, breakdown, can be defined as any modification in a part or component of a machine that prevents it from performing its function satisfactorily..
The usual states preceding a final break are, “incipient breakdown”, “incipient damage”, “deterioration” e “damage”, anyone of them, which may make the part or component unreliable or unsafe for service..
Faults can also be classified as follows:
- design deficiencies
- Material defects
- Manufacturing defects
- Assembly defects
- Conditions of service outside the project
- maintenance deficiency
- Operation errors
The table below shows the basic types of fault modes found in 99% of breakages in equipment in petrochemical units.
Classification of Failure Modes
- Deformation – plastic, elastic, etc.
- Fracture – slots, fatigue, bites, etc.
- Surface Modifications – slots, cavitation, wear, etc.
- Material changes – Contamination, corrosion, wear, etc.
- Displacements – desapertos, excessive slacks, etc.
- Leaks
- Contaminations
failure mode, not to be confused with causes of malfunction., because the first is the effect and the second the cause. The failure mode can also be the consequence of a long chain of causes., It is made, finally leading to a functional breakdown, that is, a symptom, an operational problem or insufficiency referring to a piece of equipment as a single entity.
The basic means of failures in components and machine parts are always force, time, temperature and environment, as indicated in the table below.
Causes of Breakage of Machine Components and Parts
Strength | cyclic transient static | Temperature | low ambient transient stationary cyclic |
Weather | very short short long | Ambient | nuclear chemist |
From an inspection point of view, the breakdowns are reflected in various deficiencies.
In the table below are listed symptoms typical breakdowns in the process equipment.
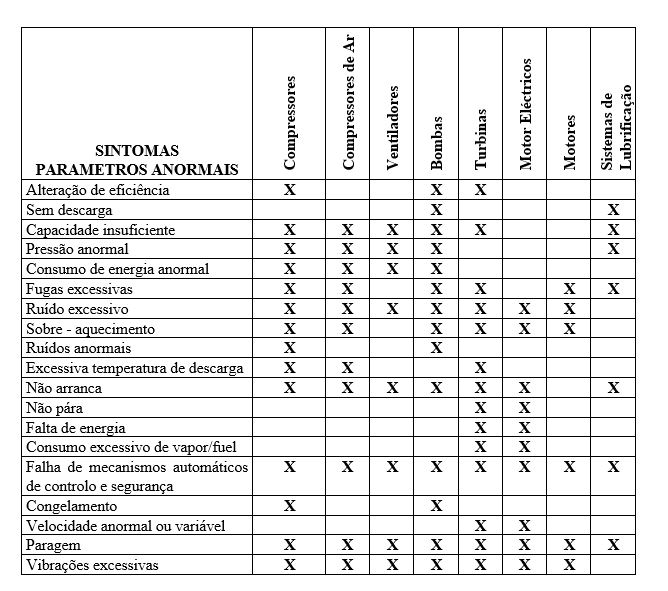
The inspection's function is to monitor the equipment in order to detect the symptoms of malfunctions.
6 – CONDITION CONTROL TECHNIQUES
The basis of a condition control system is the inspection actions that regularly take place on machinery and equipment..
these actions, where not only the inspector's senses are at stake, but also a number of specific techniques, It aims to determine the evolution of the equipment operating conditions.
Among the existing inspection techniques, you can refer for example to the following:
- Global level
- Shocks
- Frequency spectrum
– Wear Control
- Oil analysis
- Particle detectors
- Ferrography
– Temperature Control
- Thermometry
- thermography
– Noise Control
– Leak Control
Each has advantages and defects, beyond its own limitations. Its application implies, therefore, a knowledge of all the factors at play, It is common to apply more than one technique on each machine, either as a parameter to follow a trend, want to check the condition.
When selecting a control technique for a critical machine, It is important to note that the machines malfunctioned because one or more critical components fail.
Therefore, the most sensitive methods of inspection of a machine, work by detecting malfunction symptoms in individual components., since the greatest deviation from normal conditions is concentrated in these symptoms making the anomaly easier to detect.
The selection of a control method thus depends on the type of components most susceptible to failure and how this occurs.. The possible hypotheses of controlling the degradation of these components can then be considered and it may even be possible to find a single technique that can detect all types of probable malfunctions in a machine with reasonable efficiency..
On the other hand, the specific maintenance situation of each industrial unit will impose some constraints on the choice of inspection techniques to implement.
Specifically in the case of dynamic equipment, the various inspection methods can be grouped as follows.
1 – Sensory Control Machines are inspected using the human senses
2 – Performance Control The condition of a machine or component is gauged by the way in which it is performing its function.
3 – Vibration Control The condition of moving components is gauged by the size and type of vibrations generated.
4 – Particle Control The condition of critical component surfaces, subject to relative loads and movements, is evaluated by collecting and examining the wear particles generated.
The four mentioned control methods, are used, detecting the existence of a problem through the general level of the measure, and in the rate of change, while the nature of the problem can generally be determined from a more detailed analysis of the measurement results.. This is described in the table below..
The control methods described, are in fact a means of communication between the machine and the person in charge of the condition control. visual inspection, in relation to the other methods, requires minimal technical preparation, due to being performed through the inspector's senses. In other methods, means are used beyond the human senses, making interventions more complex.
It should also be noted that they are always to be used., preferably, non-intrusive parameters in systems, that is, that do not interfere with the machine process and that if possible are obtained during its operation.
REFERENCES
1 – Condition Monitoring Methods and Economics, Bruel & Kjaer
2 – Pratical Machinery Management for Process Plants VOL.2, Machinery Analysis and Troubleshooting, Heinz P. Bloch, Fred K. Geitner, Gulf P. C.