Limits of vibrations in turbomachinery
Vibration limits on turbomachinery according to ISO 20816
This article deals with the topic of vibration limits in turbomachinery, com fluid film bearings, according to ISO standards 20816.
This article is part of a series of articles included in support of Course on Vibration Limits
This article also belongs to a series, which constitutes the support material for the course on vibration analysis in turbomachinery. Links to the other articles can be found on here.
1 Machines covered
The series of ISO standards 20816 There are four rules that apply in this area:
- ISO 20816-2 mechanical vibrations – Measurement and evaluation of vibrations of the machines – Part 2: gas turbines, steam turbines and onshore generators of power greater than 40 MW, with fluid film bearings and rated speeds of 1500 rpm, 1800 rpm, 3000 r / min e 3600 rpm
- ISO 20816-4 mechanical vibrations – Measurement and evaluation of machine vibrations – Part 4: Gas turbines of more than 3 MW, with fluid film bearings
- ISO 20816-5 mechanical vibrations – Measurement and evaluation of machine vibrations – Part 5: Sets of machines in hydraulic power plants for energy production and pumped storage
The following norm, which will apply to small industrial turbines, not published yet.
- ISO/AI 20816-10 mechanical vibrations – Measurement and evaluation of machine vibrations – Part 10: Turbochargers
We thus have the machines grouped according to the following table.
Table I - Type of machines and applicable standards
turbine type | ||||
A vapor | The gas | Water | ||
Generator sets with more than 40 MW | Other turbines | Generator sets with more than 40 MW | Over 3 MW | All (fluid film sealant2) |
ISO 20816-2 | ISO 20816-101 | ISO 20816-2 | ISO 20816-4 | ISO 20816-5 |
1unpublished
2 Water machines with roller bearings, are covered by ISO 20816-3
2 Measures covered by the limits
The measures for which limits are presented, are shown in the following table..
Table II - Measures for which limits are presented
measure | ISO 20816 | ||
Part 2 | Part 4 | Part 5 | |
relative vibrations | X | X | X |
relative vibrations | X | X | X |
Variation in the level of vibrations | X | X | X |
Bearing diametrical clearance | X | X | X |
Vector | X | X | X |
Temperature | X |
3 Vibration limit zones
The vibration limit zones are those shown in the table below..
Table III - Vibration limit zones
ISO 20816-2 | ISO 20816-4 | ISO 20816-5 |
A | A | |
B/C | B/C | A/B |
C/D | C/D | C/D |
D | D | D |
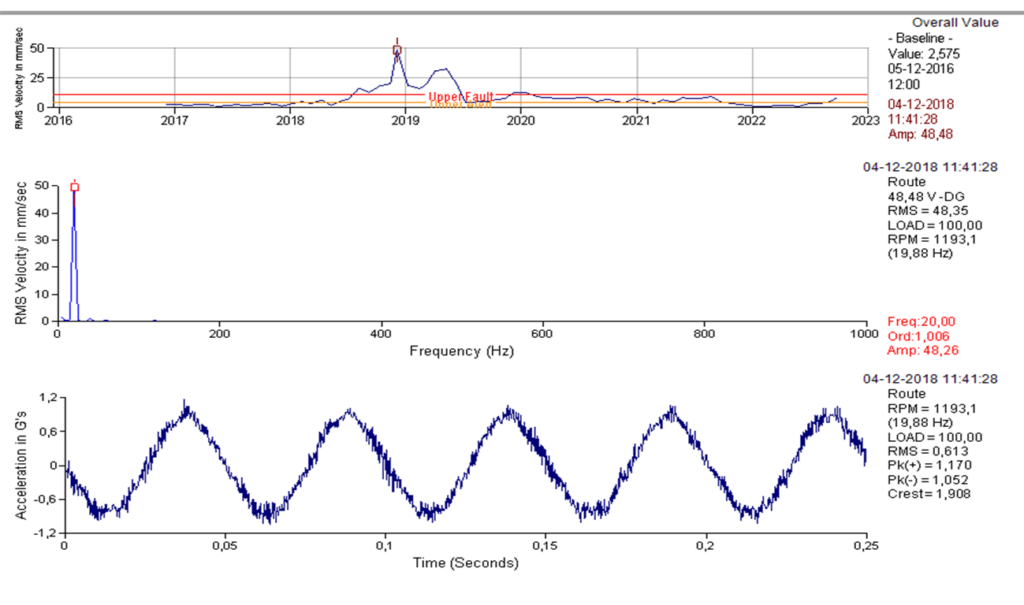
Limits of vibrations in turbomachinery – Figure 1 – Vibration levels exceed predefined limits
4 Limits of vibrations in turbomachinery – Variation in the level of vibrations
These three standards recommend that an alert be established when the variation in the vibration level is 25%, or more.
A 20816-5 also recommends that if a phase variation greater than 30% investigate what is happening.
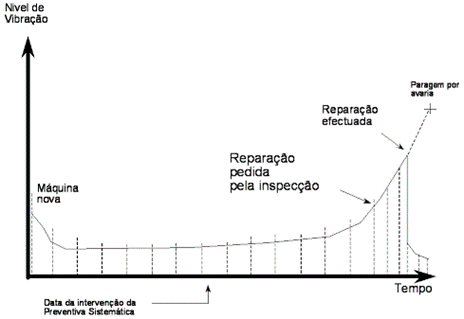
Limits of vibrations in turbomachinery – Figure 2 – Variation of the amplitude of vibrations
5 Limits of vibrations in turbomachinery – Diametric clearance of bearings
All three standards recommend limiting peak-to-peak displacement vibrations., measurements with proximity sensors, relative to the diametrical clearance of journals in flow-film bearings. These limits are referred to in the table below.
Table IV - Limit of vibrations in peak-peak displacement in percentage of the diametral gap
ISO 20816-4 / ISO 20816-2 | ISO 20816-5 | |
A/B | 40% of the diametric clearance | |
B/C | 60% the diametral B fold | |
C/D | 70% of the diametric clearance | 70% of the diametric clearance |
D | D | D |
6 Limits of vibrations in turbomachinery – Vector
The three standards refer to what is contained in the ISO 20816-1 about this theme, as mentioned below.
“The evaluation considered in this document is limited to broadband vibration without reference to frequency or phase components.. That's it, in most cases, suitable for acceptance testing and operational monitoring purposes. However, in some cases, the use of vector information for vibration evaluation, may be desirable, on certain types of machines.
The vector change information, are particularly useful in detecting and defining changes in the dynamic state of a machine. In some cases, these changes would not be detected when using wideband vibration measurements.”
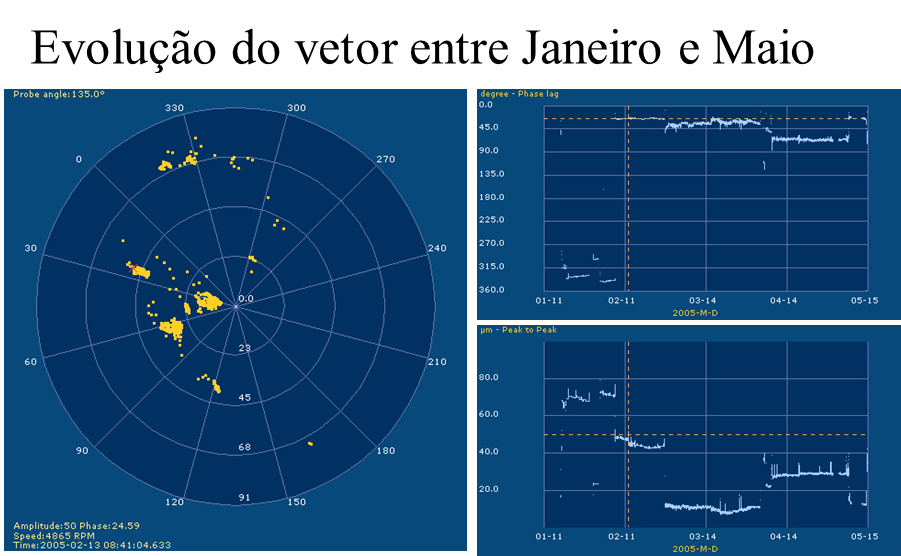
Limits of vibrations in turbomachinery – Figure 3 – Phase variation related to the position variation of a loose impeller on the shaft, in a turbo pump.
7 Temperatures
The only standard to mention temperature limits is the one referring to water machines, that is, a 20816-5.
8 Example – Vibration limits on a vertical hydro generator, like turbine Francis, of the Group 4, according to ISO 20186-5
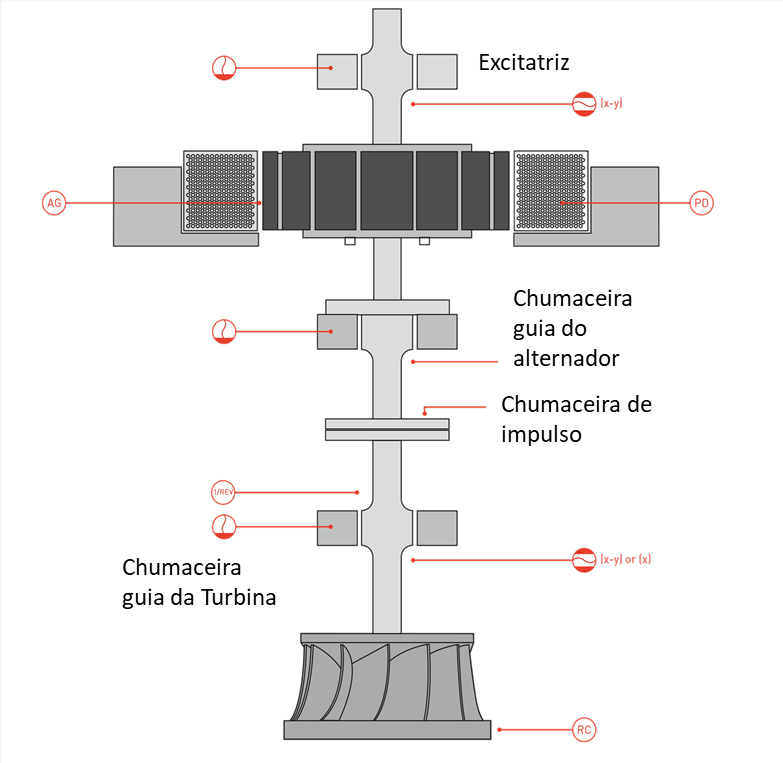
Limits of vibrations in turbomachinery – Figure 4 – Francis generator set
Operation within rated machine conditions
For this type of machines, the vibration limits are those that can be seen in the table below.
These limits are independent of height and flow rate., and are valid for when the machine is operating within its normal operating regime. For Francis groups, with vertical shaft, the normal operating range is 70% a 100 %, of rated power.
It is essential to perform relative shaft and absolute bearing vibration measurements to obtain a good assessment of the condition of the machine and the possibility of failure..
Table V - Vibration and temperature limits for generator sets with Francis turbine and vertical shaft (Group 4)
5 Francis vertical | Relative shaft vibrations Sp-p , μm | Bearing housing vibrations vrms , mm/s | ||
Turbine | Generator - Turbine side | Turbine | Generator - Turbine side | |
action limit 1 (A-B/C) | 180 | 180 | 0,9 | 0,5 |
Vibration level variation | >25% | |||
Variation of the vibration phase to 1 x RPM | >30º | |||
Limits of 70% the diametric clearance of the bearings | 440 μm x 70%=308 μm | 540 μm x 70% = 378 μm | – | – |
chumaceiras temperature | See explanation below | |||
action limit 2 (C/D) | 280 | 280 | 1,4 | 0,8 |
The meaning of the various limits is as follows:
Zone A-B: Machines with vibration values that do not exceed Action Limit I, are considered acceptable for long-term operation, no restrictions; assuming there are no other indications of problems such as high bearing temperature exceeding defined limits, or the relative displacement of the shaft to be exceeded 70% cold bearing diametral clearance.
zone C: Machines with vibration values in this zone indicate either further investigation or some action to reduce vibrations.. The first parameters to be investigated should be the temperature of the bearings, or the relative displacement of the shaft to be exceeded 70% cold bearing diametral clearance.
zone D: Vibration values in this zone, indicate that there is a probability of damage to the machine. IS, therefore, Immediate action required to identify causes for high vibration levels.
The following flowchart shows how zone boundaries can be used to identify if further investigation and/or action is required.
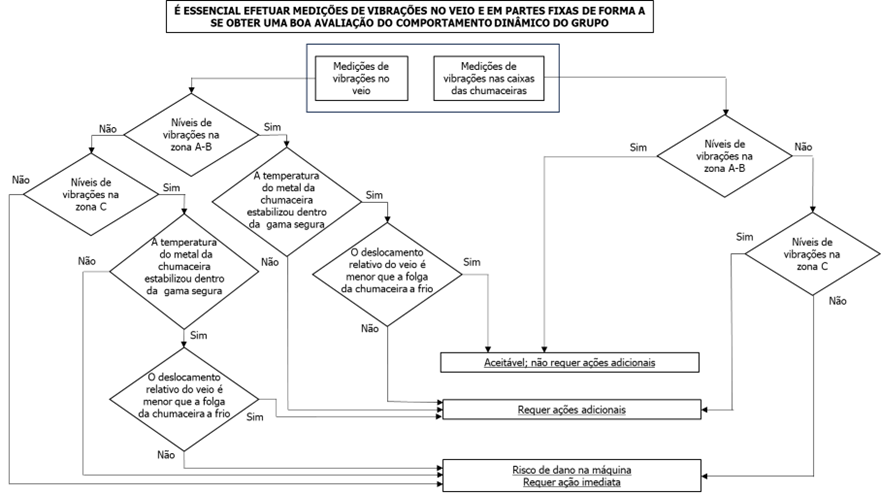
Limits of vibrations in turbomachinery – Figure 5 – Flow diagram showing how zone boundaries can be used to identify if further investigation and/or action is required
Limits of 70% the diametric clearance of the bearings: When shaft vibration is greater than 70% cold bearing diametral clearance, this indicates that there is a high probability of damage to the machine.
Vibration level variation: Actions will be taken when the action limits indicated in Table V are exceeded. Continued operation at these vibration levels may be permissible., if there has been no history of problems with the machines and the vibration levels have not changed. Yet, if there is a change in the level of vibrations (>25%) of the shaft and/or bearing, investigation is recommended. A significant change in measured vibration requires action even if the action threshold (A-B/C) has not been hit.
Variation of the vibration phase to 1 x RPM: A change in phase is considered significant. (>30°) of the vibration signal, in relation to previously established reference values (that is, taken less than 3 months before change detection), particularly if the changes are sudden.
These limits are independent of height and flow rate., when the machine is operating within its normal operating regime.
Bearing temperature: According to the rule mentioned, for all defined vibration thresholds, the following applies:
- in the guide bearings, the stabilization temperature of conventional antifriction metal, must be less than 65 °C; in most machines the temperatures stabilize around 50 °C;
- On thrust bearing, the stabilization temperature of conventional antifriction metal, must be less than 85 °C; in most machines the temperatures stabilize around 70 °C;
- Temperatures higher than mentioned may be acceptable, but require justification or investigation by the supplier.
Operation outside the rated conditions of the machine
Attention should be paid to the following operating conditions where high levels of vibration may occur namely, steady state with partial load, in overload, and during transient operating conditions during start-up and shutdown.
Evaluating measurements under any of these conditions is much more difficult than, for normal measurements operating within design conditions. At the moment, the available data are insufficient to establish limits for these special operating conditions.