Steam traps inspection
For a good management of a steam network is essential to make, regularly, a inspection of steam traps.
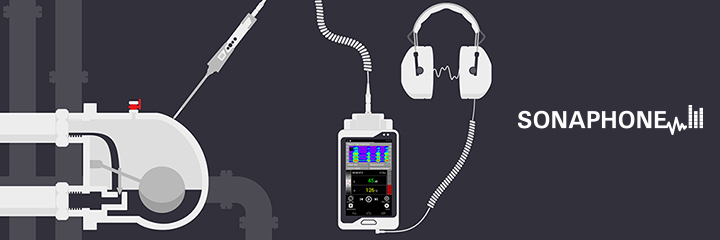
A major contributor to waste and inefficiency are leaks, both in atmosphere and in valves and steam traps. According to the US Department of Energy, a typical installation can save 20% steam, improving their steam system. It is common knowledge that, if the steam traps do not have proper care, to one fifth of the steam generated in a central boiler, It is lost through leakage or failure of steam traps.
The goal of a program, Successful, traps inspection must repair any defective steam trap and steam leak that may affect safety, reduce energy waste, promote sustainability or affecting product quality.
steam traps are automatic valves, designed to discharge condensate (and would eliminate) without steam loss. Like this, as any mechanical equipment, They are subject to wear which will eventually require maintenance and replacement, according to the manufacturer's specifications. Faults usually take two forms:
- Steam leakage, or
- condensate discharge lock (i.e., cold traps)
To perform the inspection of steam traps are used several methods to determine if they are functioning properly, including:
- visual observation;
- Temperature Measurement;
- sound measurement / vibration
- ultrasound measurement
- Any combination of these methods.
Inspection of steam traps by visual observation
Although limited as steam traps inspection method, visual observation is an important first step to determine whether a trap is properly operating, or not. For example, certain visual signals, such as the absence of any condensate discharge end or steam leakage, to be discharged from the trap, It may indicate the need for repair of the trap. However, it is clear that visual analysis is limited to inspection of steam traps, in systems with open outlet. for cases, in which systems recover condensate in a closed pipe, the pipeline will prevent visual diagnosis. In some cases, the installation of a display in the trap output can assist in visual indication.
The steam trap inspection can also be accomplished externally through a hole or joint connection. In most cases, unless the condition of the problem can be clearly determined visually, steam traps inspection methods will be required by the sounds, ultrasound and temperature, in some cases, by thermography, to provide the correct diagnosis.
steam traps by the inspection temperature
A condensate trap in the temperature measurement inlet is the first step in the steam trap inspection process temperature. Except in cases of intentional cooling, the condensate in the trap inlet temperature should be close to the temperature of saturated steam.
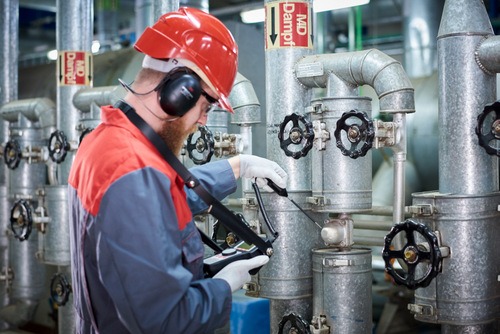
steam traps by the inspection temperature – Traps cold (locked)
The temperature can be extremely useful when you are trying to determine whether:
- A trap is blocked
- Its capacity is insufficient
This is because these problems cause condensate accumulation, lowering the temperature of the steam trap. If the temperature is significantly low and the line where the steam trap is in service, Low Temperature traps generally indicates:
- A trap undersized, seat (hole) Incorrect pressure to trap;
- A discharge failure due to trap / filter blocked;
- A negative pressure differential condition, in the case of equipment to be powered through a control valve (a condition that occurs when a differential pressure dewatering device, as a trap, becomes negative and does not allow for the discharge of condensate through the drain device, causing flooding within an exchanger, rather than drain it .., for example).
Find steam leaks through temperature?
The inspection of steam traps, By measuring temperature, to determine whether a steam trap is leaking or not, can lead to a wrong conclusion. This is because, a condensate with a higher temperature in vapor form reevapora, when introduced into a system with lower pressure. As the temperature of the vapor is the same live steam to leak, can not differentiate between a regular escape of steam and condensate discharge, by measuring temperature. A report from the wrong condition, based on temperature, can lead to a substitution, not necessary, a steam trap, In good conditions.
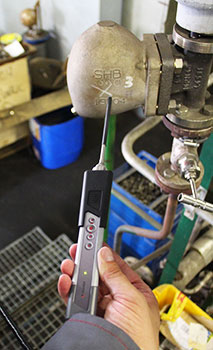
Steam traps inspection by the sound
The condensate flowing through a trap produces sound and vibration, caused by the opening and closing mechanism of most traps. When a trap is not operating as desired (due to wear, blockage or other reason), often these sounds change. The recognition of these differences, It may be a method for inspection of steam traps.
In inverted bucket steam trap, for example, scum and other floating debris can block the hole eliminator air, which in turn, Because the blockade of the inverted bucket, at least temporarily, leading to blockage of the discharge of the condensate and freeze in certain environments.
The live steam leaking from the trap, It can also produce a distinct sound, which can be explained by comparing the difference between “a whistle and a wave.” A whistle is a loud sound generated by steam, even generated smoothly. It is impossible to duplicate the same kind of sound through a liquid, This is a large amount, as a wave, or small, as a drop out of a faucet.
The condensate must be flowing normally through the trap and the sound must have a lower tone. So, if this sound change and appear to be closer to the sharp tone as the steam flow, then the trap can have a large amount of flash steam or may be live steam to leak and must be inspected in detail.
Tools for inspection of steam traps
Inspection of steam traps for measuring temperature
They can use several tools to steam traps inspection, By measuring temperature, as, or a combination of both. Inspect a trap, only the temperature, requires that the temperature sensor is specifically positioned at the trap entrance and the exit no.
For example, even if the steam temperature at the inlet, be of 250 °C, the condensate is discharged into the atmosphere is eliminated, then the temperature in the steam trap outlet will not increase more than 100 °C. Therefore, even if the steam is leaking, you can not make a correct diagnosis of the condition of the steam trap. The best temperature is used to determine whether traps are block the discharge of the condensate and not to detect steam leakage.
The most modern instruments, used for measuring the temperature, They have a thermocouple and a digital display for easy use and more accurate readings. However, to provide more precise information, for both blocking and leak conditions, the instrument should be provided with temperature measurement and the sound / ultrasound level.
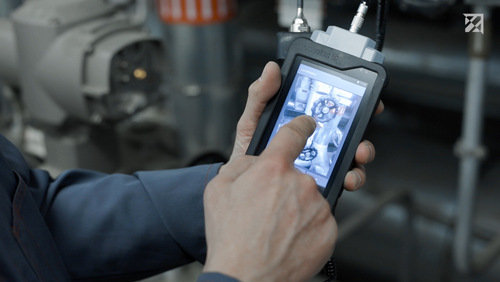
The inspection of steam traps through som
To expand the sound into a trap can be used stethoscopes . Although they do not have the same precision of modern electronic instruments, its portability and ease of use, can make them useful equipment when combined with the most modern inspection equipment. The point where the stethoscope tip is pcolocad will depend on the type of sound that the inspector is trying to listen and generally requires that the inspector check several points.
The use of ultrasound meters
Of course, using an ultrasonic meter will provide greater accuracy, inspection of steam traps, than with a stethoscope.
As mentioned above, instruments measuring temperature and are ideal ultrasound. The temperature reading is necessary to determine whether the trap is or is not locked and ultrasound is the preferred method to check for leaks steam. Effectively a steam leaking sound is significantly different between steam and condensate.
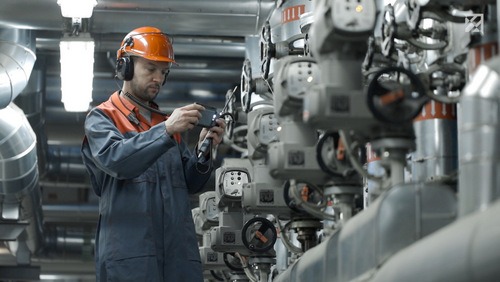
When ultrasound is properly filtered, these instruments, made temperature ultrassons, They can provide a consistent and accurate reading, allowing a trial of steam trap condition. Some diagnostic tools based on ultrasound, They can even make a judgment of the condition by automatically comparing the measured result, with the previously known conditions and improve well, significantly, the evaluation of precision.
The steam trap inspection equipment ultrasound, is the diagnostic tool more versatile steam systems and needs, currently available. The ultrasonic meter allows the operator to hear sounds not noticeable to the human ear. This type of equipment is a high-frequency signal (typically 20 – 100 KHz) and the signal heterodiniza, providing an audible sound to hear the operator with the aid of headphones. The inspection of steam traps ultrasound is the ultimate test method to be used in the steam trap testing program to detect defective steam traps. The operator uses the stethoscope module to contact the discharge side of the steam trap and has the ability to detect even small changes in operating characteristics or malfunctions. The sensitivity of most high measuring equipment frequênci,the allows the technician to listen not only steam traps completely does not work (blowing steam), but even the steam escape from a trap in normal operation. This test method provides the first steam trap wear signal and is used as a predictive tool for steam traps condition control. The ultrasonic test allows the technician responsible for testing hear the internal operation of the steam trap. Like this, the effectiveness of the trap operation, It can be determined. To hear ultrasound test unit, It has to take into account that the condensed steam will sputter and beeps during the test with the ultrasound equipment.
recommendations
The steam trap inspection is an important part of traps park management of an installation. Once the failure is confirmed, the trap must be repaired or replaced as soon as possible, for greater profitability.
For an accurate diagnosis of the condition of the steam trap, It is essential to get help from an experienced technician with specialized equipment. For these reasons, it is highly recommended that this equipment is capable of measuring temperature and ultrasound.
In addition to the trap itself, It is also important to inspect the peripheral equipment including manual valves, válvulas bypass, check valves and the operating condition of equipment using steam. Thus, regular optimization of the steam system can help maximize process efficiency and often, lead to significant energy savings.