Vibration analysis compressors
Vibration analysis compressors
This article describes two cases of actual Vibration Analysis compressors.
Case 1 – Vibration analysis compressors – supercharged
A compressor, similar to that shown in Figure 1, It is part of a Predictive Maintenance Program since the year 2007, It is subject to quarterly inspections with a vibrométricas vibration analyzer.
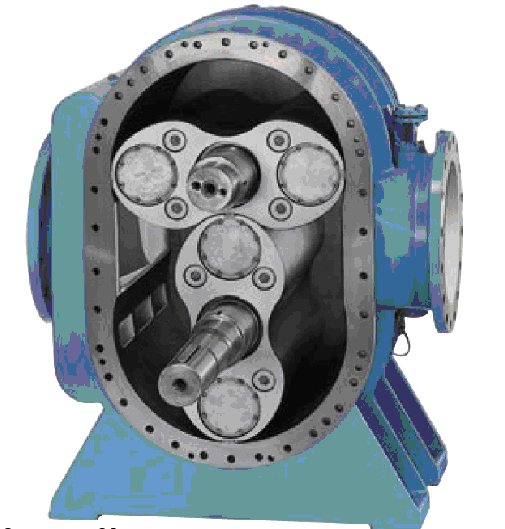
Figure 1 - Vibration analysis compressors – Compressor scheme
Case 1 - Initial situation
Almost from the beginning of inspections, vibrométricos data collected in the support shaft of the compressor client, the drive side, They revealed the presence of frequency associated with defects in the inner ring raceway bearing installed (Figure 2). Yet, since the amplitudes were recorded characteristics of an early stage of development of the abnormality, it was decided to continue to monitor this condition until its evolution justify maintenance work.
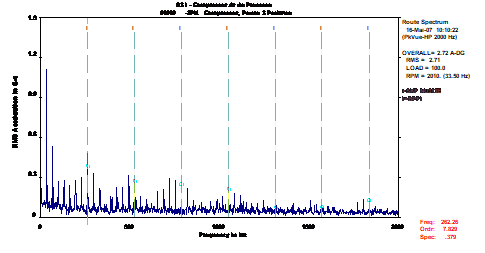
Figure 2 - Vibration analysis compressors- PeakVue spectrum collected in the principal support shaft, the drive side, collected inspection May 2007.
Case 1 - August inspection
Inspection made in August 2008, observed a deterioration of the parameters for monitoring the operating condition of the compressor bearings (Figure 3).
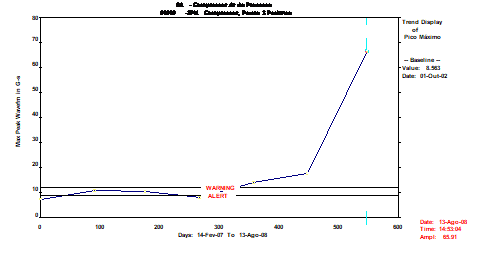
Figure 3 - Vibration analysis compressors – Evolution parameter Peak Maximum of PeakVue waveform during the various inspections.
Case 1 - Rolling Photography
Given the great progress registered in all the defined parameters, We were required to intervene to replace the compressor bearings. In intervention performed it was found that the shaft bearing the compressor inlet, the drive side, showed significant degradation in the inner ring raceway and the cage match is found (Figure 4).
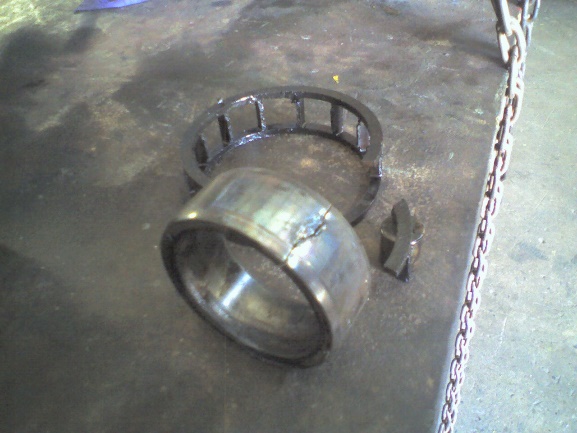
Figure 4 - Vibration analysis compressors – Inner ring and bearing cage substituted
Case 1 – Conclusion
As it was expectable, after the intervention performed, there was a significant decrease in generalized and set parameters for controlling the operating condition of the bearings. With monitoring of the condition, by measuring and analyzing vibrations, it is possible to identify in advance the development of faults, monitor its progress and schedule maintenance work on equipment, minimizing maintenance costs.
Case 2 – Vibration analysis compressors – screw air compressor Atlas Copco GA180
Because of their criticality, It was integrated into the established predictive maintenance program, an air compressor Atlas Copco GA180. As often happens with this type of machines, The greatest difficulty arises for monitoring the operating condition and by measuring vibration analysis, It relates to the failure to know the technical data necessary to characterize the machine characteristic frequencies.
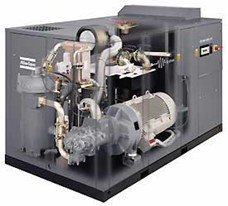
Not being this exception case, de facto, relevant information as reference bearings installed in the compressor element, number of teeth of the gears and rotation speed of each screw, not available, thus making it more difficult the work of analysis of data vibrométricos.
Case 2 – Result of the first inspection
Immediately after completion of the first scheduled inspection vibrométrica, analyzing the data recorded in the motor support opposite the drive, It revealed the presence of frequencies associated with developmental abnormalities in the bearing installed (Figure 6).
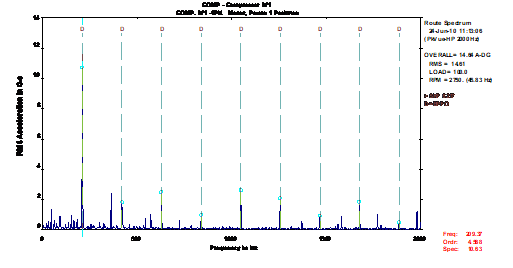
Figure 6- Case 1 – Vibration analysis compressors – supercharged – PeakVue spectrum recorded in the engine support
However, More disturbing than the fact that they have been identified the frequencies mentioned above, was the fact that the parameters for monitoring emissions of high frequencies present in the compressor element, in a general way, values higher than those considered normal for this type of equipment. For example, Maximum Peak parameter of the form Where reached values 58 g's while the parameter that measures the level of vibration in the 1kHz-20kHz band reached values 24 g´s Pico.
In addition to the levels reached by these parameters, also PeakVue spectra recorded at the measuring points defined in the compressor element, registavam the presence of frequency 238,84 Hz and harmonics (Figure 7). As said before, the lack of technical machine data does not allow to clearly identify the source of the frequency. Yet, the dynamic characteristic of the compressor and the knowledge gained about the behavior of this type of machines, led to suspect that the frequency of 238,84 Hz was non-synchronously, whereby it would not be the pulsating frequency, which is characteristic of this type of machines.
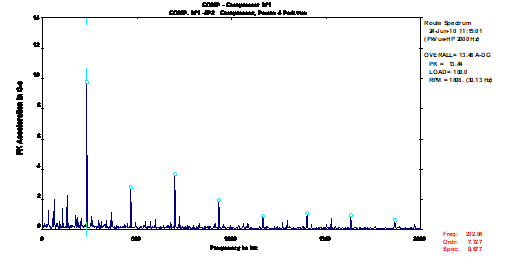
Figure 7 Case 1 – Vibration analysis compressors – supercharged – PeakVue spectrum registered in the compressor element
Case 2 – recommendation made
In view of all the foregoing, It recommended the overhaul of the machine, including the replacement of motor bearings.
Case 2 - Measurements after intervention
In scheduled inspection conducted after the review machine was found:
- The disappearance of the frequencies associated with the development of abnormalities in motor bearings (Figure 8);
- The significant decrease of the amplitudes of the set parameters to monitor emissions of high frequencies in the compressor element;
- The disappearance of frequency 238,84 In Hz and harmonic PeakVue spectra collected in the compressor element (Figure 9).
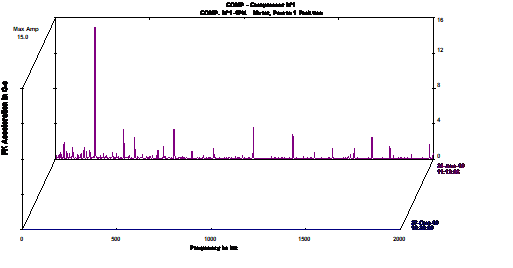
Figure 8- Case 1 – Vibration analysis compressors – supercharged – PeakVue spectra recorded before and after the replacement pain motor bearings
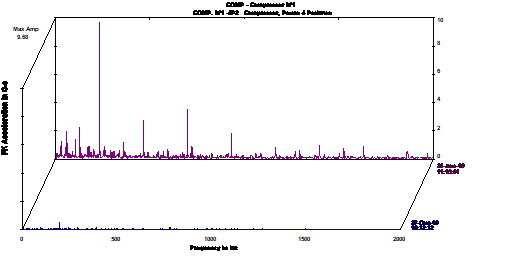
Figure 9- Case 1 – Vibration analysis compressors – supercharged – PeakVue spectra recorded before and after the revision of the compressor element
Case 2 – Conclusion – Screw Air Compressor
Despite the lack of technical data that allow characterize the typical machine frequencies, by monitoring parameters of the vibratory, it is possible to identify in advance the development of anomalies, preventing the occurrence of catastrophic failures and to minimize maintenance costs.