Analysis of electric motors in mines
The subject of this article is the identification of faults in machines, through the analysis of electric motors in mines, with the MCM technique.
The MCM Monitoring System
O MCM (Electric Motors Condition Monitoring) is a recent electric motor analysis technology, that works based on Artificial Intelligence that compares the real engine, to be monitored, with a mathematical model of the engine, running up to 600 different load conditions. This mathematical model is obtained from a learning period lasting a few days.
The MCM monitoring and diagnostic system is also designed to detect electrical faults in engines, in response to limitations of vibration monitoring. In addition to the electrical failure modes, also detects mechanical failure modes the engine or driven machinery.
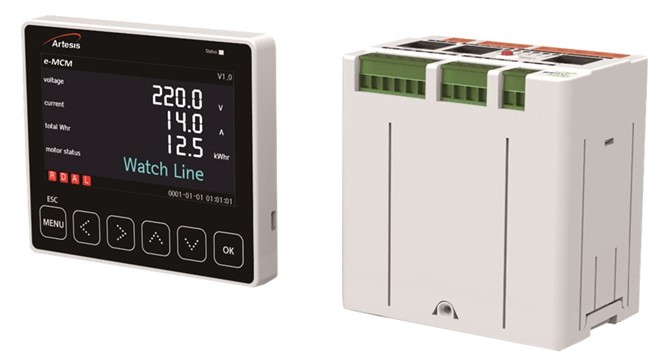
Working principle
To carry out the analysis of electric motors the MCM monitor uses a combination of dynamic voltage and current waveforms, along with learned models, to detect faults in the motor or the driven equipment. Learning is supported by an additional database, if the monitor has been installed in an already faulty engine. The monitor detects differences between the observed current characteristics and the characteristics learned and relates these differences failed.
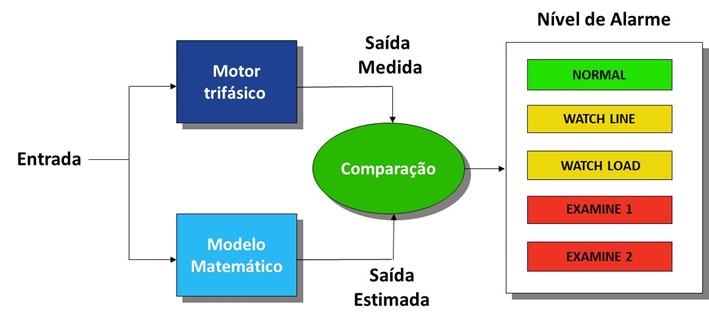
Engine fault detection is based on an engine model, learned by the monitor, physics-based, wherein the constants in the model are calculated from data in real time and compared to values previously learned.
Mechanical failure detection is based on spectral power density amplitudes. (PSD) in specific frequency bands, in relation to the learned values. This information is automatically combined with specialized knowledge in diagnosis. Because of this spectral band approach, mechanical fault detection provides guidance for a class of possible failures. Sensitivity to some flaws (for example, bearing failures of the rolling elements) decrease with distance from the component fails pathways. On the other hand, failures that increase engine load are independent of distance from the engine.
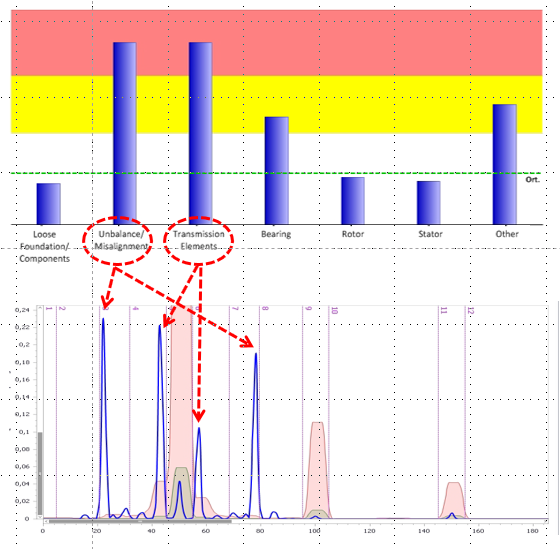
The report
The report is issued automatically by the system, without the need for interpretation of an expert.
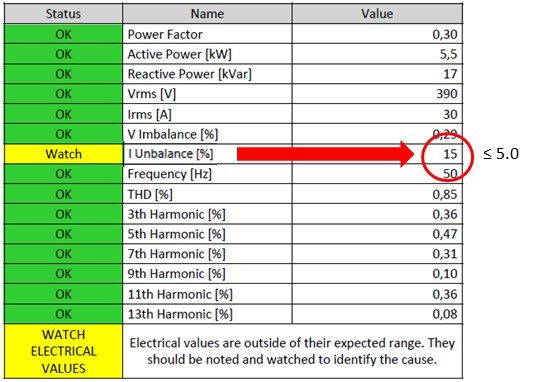
Analysis of electric motors in mines – case study 1 – Identification of damage to a mine conveyor belt
The MCM system has detected a decrease in load on the process side of the conveyor belt. The maintenance team confirmed that the belt scraper was worn and did not exert enough force in the process.
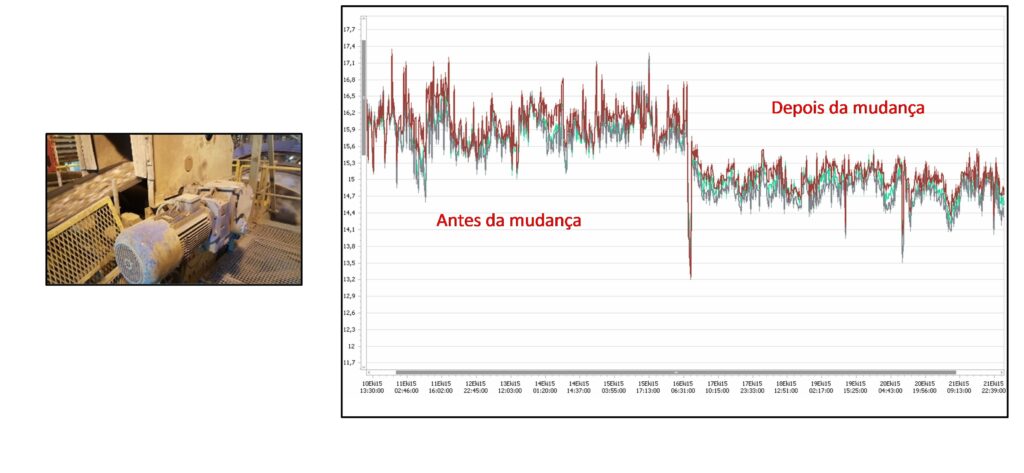
Analysis of electric motors in mines – case study 2 – Mixer pulley failure
MCM detected an anomaly in the transmission equipment (belt/pulley malfunction). Malfunction observed during the learning phase. During the maintenance intervention, the team replaced the belt and aligned the pulley.
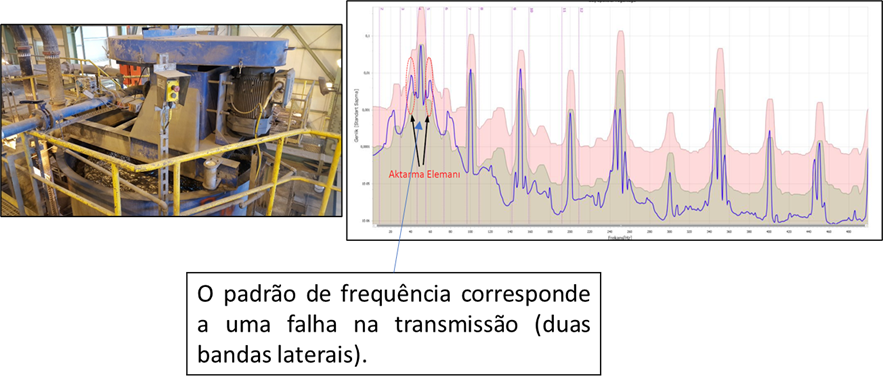
Analysis of electric motors in mines – case study 3 – Fault in mixer bearing
MCM detected an anomaly in the transmission equipment (belt/pulley malfunction). Malfunction observed during the learning phase. The maintenance team replaced the belt and aligned the pulley.
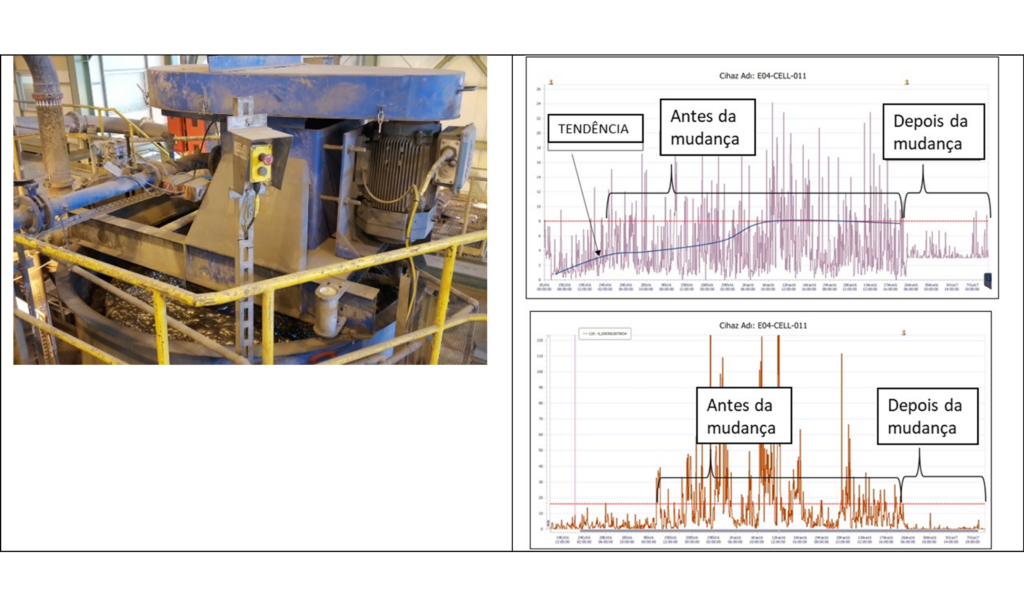
Wear marks and scratches were observed on the outer ring and balls.
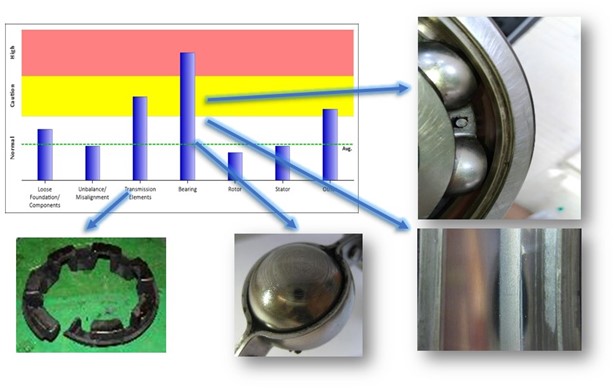